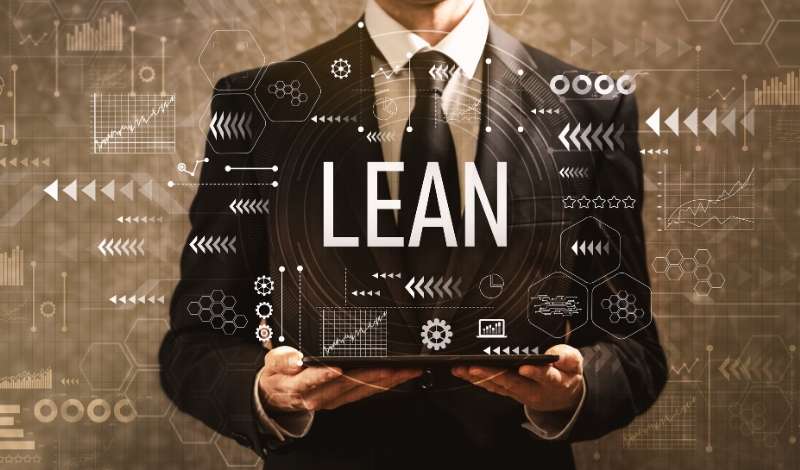
Professional racing epitomizes the pursuit of efficiency. Teams are intensely opposed to any form of waste.
Every fraction of a second during a pit stop is meticulously planned in racing. Each part of the vehicle undergoes thorough analysis to guarantee peak performance. Race strategies are crafted to optimize speed and minimize time from start to finish.
Applying this high-efficiency mindset to industrial maintenance leads to lean maintenance. Lean maintenance is a stringent approach that focuses on relentlessly reducing and eliminating waste in every aspect of maintenance operations. This approach aims to enhance speed and efficiency while reducing costs.
This guide provides fundamental insights into developing and assessing a lean maintenance strategy.
What Is Lean Maintenance?
Like lean manufacturing, lean maintenance involves continuously identifying, minimizing, and eliminating inefficiencies in maintenance tasks. Any element that doesn’t enhance output, reduce expenses, or improve productivity is considered wasteful.
Numerous instances of waste can be found in maintenance processes, such as:
- Expenditure on parts that become outdated before use
- The time utilized in clarifying the specifics of a maintenance request
- Efforts in gathering maintenance data that remains unused
Recognizing waste within a maintenance program can often be challenging. This is where iteration becomes crucial in a lean maintenance strategy. Iteration refers to implementing incremental changes over time to discover the most efficient way to organize processes and tasks.
Therefore, lean maintenance is not a singular, complete project. Instead, it’s a mindset and approach that evolves and strengthens over several years.
Why Is Lean Maintenance Important?
Chances are high that you’ve recently said something like, “That was a complete waste of time,” or “That was a total waste of money.” Lean maintenance aims to eradicate such instances.
Although there could be countless scenarios to which these phrases apply, they typically align with four primary advantages:
- Cost Savings: Lean maintenance significantly reduces expenses by optimizing resource utilization and minimizing wasteful practices. This leads to lower operational costs and increased financial efficiency.
- Efficiency Gains: This approach streamlines maintenance processes, reducing time spent on unnecessary tasks. It results in quicker turnaround times and more productive workflows, enhancing operational efficiency.
- Maximized Potential: By focusing on essential tasks and eliminating redundancies, lean maintenance ensures that equipment and personnel operate at their full capacity, improving performance and productivity.
- Employee Management: Lean maintenance fosters a more engaged workforce by reducing unnecessary workload. It allows employees to concentrate on high-value activities, enhancing job satisfaction and promoting a more skilled and efficient team.
Three Types Of Waste In Lean Maintenance
Identifying waste is crucial for its elimination. Waste typically manifests in three key areas in maintenance operations: environmental, financial, and human potential.
- Environmental Waste: This refers to the unnecessary consumption or misuse of resources, leading to environmental harm. It includes excessive energy usage, improper disposal of materials, and inefficient recycling practices.
- Financial Waste: Financial waste involves mismanagement of funds and resources, resulting in unnecessary expenses. This can be due to overstocking parts, investing in underutilized equipment, or inefficient maintenance practices.
- Human Potential Waste: This type of waste occurs when the skills and abilities of the workforce are underutilized or mismanaged. It includes assigning skilled workers to mundane tasks, inadequate training, or failing to harness their full potential and creativity.
Developing a Maintenance Lean Mindset
Establishing a maintenance lean strategy is crucial in initiating the correct inquiries, reassessing existing methods, and embracing adaptability. This approach, known as a maintenance-poor mindset, is vital for the long-term success of lean maintenance strategies.
Four critical adjustments are necessary for transitioning to a maintenance lean mindset:
- Detail to Overview: Shift focus from minute details to understanding the overall picture. This involves seeing how each small part fits into the larger scheme of the maintenance process.
- Action to Data Collection: Instead of just completing tasks, prioritize gathering data during the process. This helps in making informed decisions and improving future maintenance work.
- Gradual Changes: Move away from making significant, sweeping changes. Embrace incremental, iterative improvements that allow for continuous refinement and adjustment.
- Questioning the Norm: Replace the mindset of accepting things as they are with a habit of asking about their necessity. This encourages constant reevaluation and optimization of processes.
Developing a Lean Maintenance Strategy
The construction of a lean maintenance strategy involves a three-stage approach:
- Analyzing Current Practices: Start by comprehensively understanding your existing maintenance activities and their execution methods.
- Identifying and Removing Waste: Pinpoint areas of inefficiency and actively work towards eradicating them.
- Establishing Continuous Improvement Processes: Implement systems that enable the consistent repetition of the first two steps, ensuring ongoing refinement and efficiency.
Step 1: Assessing Your Current Maintenance Practices
The initial phase involves thoroughly analyzing your team’s current maintenance operations to identify areas of excess or insufficient work.
This assessment includes:
- Equipment details like criticality and failure modes.
- Regular inspection and repair schedules.
- Emergency response protocols and team reactions.
- Process for creating, assigning, and tracking follow-up or corrective maintenance.
- Activities and outcomes of team meetings.
- Setting goals, establishing metrics, reporting, and data collection methods.
- Health, safety, and compliance-related practices.
- Management of parts purchasing and storeroom.
Additionally, it’s important to consider health, safety, compliance protocols, parts purchasing, and storeroom management. Beyond internal processes, it’s crucial to align with:
- Seasonal variations in production levels.
- Periods of high and low sales.
- Adaptive measures for past emergencies.
- Overall organizational goals and available resources.
Step 2: Identifying Primary Improvement Opportunities in Maintenance Lean
In the context of maintenance lean, it’s essential to pinpoint areas for immediate enhancement. This involves:
- A detailed analysis of current maintenance practices to identify inefficiencies and sizes that can benefit from quick optimization.
- By focusing on tangible, actionable changes, such as streamlining workflows, reducing downtime, or improving resource allocation, you can create significant impacts in the short term.
- This step is about taking proactive measures to refine processes, boost efficiency, and reduce waste, thereby setting the stage for more substantial, long-term improvements in maintenance operations.
Step 3: Building a Long-Term Vision
Developing a long-term vision is crucial for sustaining improvements and achieving enduring efficiency in lean maintenance. This vision should encompass a comprehensive strategy that aligns with the organization’s goals and addresses future challenges and opportunities.
It involves setting ambitious, achievable targets, such as advancing technological integration, fostering a culture of continuous improvement, and developing a skilled workforce adept in lean practices.
This long-term perspective is about maintaining the status quo and continuously evolving and adapting to new trends, innovations, and industry best practices, ensuring that the maintenance lean approach remains practical and relevant.
Conclusion
Fundamentally, lean maintenance involves aligning maintenance activities with the broader objectives of the business. While this approach may initially cause some disruption, it’s a vital transition in transforming maintenance from being perceived merely as an expense to being recognized as a critical contributor to value creation.
Achieving this shift allows the maintenance team to be regarded as an essential partner in the business, opening up new opportunities and perspectives on how their role is valued and understood.
Read more: What Are The Best 10 Lean Tools? Understand Their Benefits