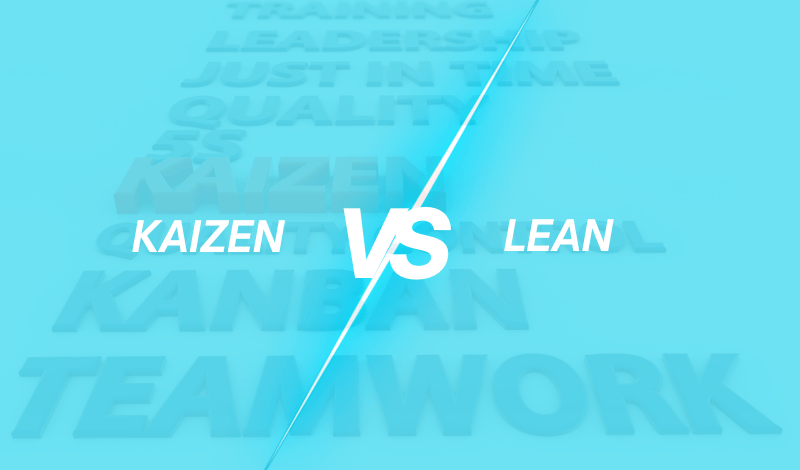
“Kaizen vs. Lean” represents a pivotal debate in the dynamic world of continuous improvement. Kaizen, a Japanese philosophy, emphasizes gradual, constant change, focusing on efficiency and waste reduction.
Lean, originating from the Toyota Production System, also aims for efficiency but strongly emphasizes optimizing the entire process flow. Together, these methodologies revolutionize businesses unexpectedly, transforming processes, workplace culture, and employee mindset.
Continue reading this blog to learn more about Kaizen vs Lean.
What is Kaizen?
Kaizen, a Japanese term meaning “change for better,” is more than just a methodology; it’s a philosophy that encourages continuous, incremental improvement in all aspects of life, particularly in business processes.
Rooted in post-World War II Japan, Kaizen became a cornerstone in Japanese management practices, eventually gaining worldwide recognition for its effectiveness in operational excellence.
The key principles of Kaizen include:
- Good Processes Bring Good Results: Focus on refining processes, and the results will follow.
- Go See for Yourself to Understand the Situation (Genchi Genbutsu): Direct observation is crucial for proper understanding.
- Speak with Data, Manage by Facts: Decisions should be data-driven and factual.
- Take Action to Contain and Correct Root Causes of Problems: Addressing the source of problems is essential for long-term improvement.
- Work as a Team: Emphasizes collaboration and cross-functional teamwork.
- Kaizen is Everybody’s Business: Involvement of all employees, from the CEO to the shop floor workers.
Real-world examples of Kaizen include Toyota’s implementation of the Just-In-Time production system, dramatically reducing waste and improving efficiency.
Hospitals worldwide have adopted Kaizen for patient care processes, significantly improving patient satisfaction and safety. Many service industries, like banking and hospitality, use Kaizen to enhance customer service and operational efficiency. These examples showcase Kaizen’s versatility and its impact across various sectors.
What is lean?
Lean, a term synonymous with efficiency and waste reduction in business processes, originates in the Toyota Production System (TPS). Developed by Toyota in Japan in the mid-20th century, Lean methodology revolutionized manufacturing and production.
The TPS aimed at improving efficiency, reducing waste, and increasing productivity. This approach soon spread from Toyota to other Japanese companies and eventually globally, becoming known as ‘Lean.’
The core components of Lean methodology include:
- Value: Identifying what truly adds value from the customer’s perspective, ensuring that every process aims to deliver this value.
- Value Stream Mapping: Analyzing and designing the flow of materials and information required to bring a product or service to a customer.
- Flow: Ensuring smooth and uninterrupted progression of processes, eliminating delays, and ensuring products or services flow seamlessly to the customer.
- Pull System: Production driven by customer demand, ensuring that nothing is made without a pull from the downstream process or customer, reducing overproduction and inventory.
- Perfection: Continually improving processes and striving for perfection in production, leading to high-quality products and services.
- Respect for People: Engaging and empowering all employees, respecting their contributions, and encouraging continuous improvement and development.
- Continuous Improvement (Kaizen): Constantly seeking ways to improve processes and reduce waste.
Lean’s influence has extended far beyond manufacturing, impacting sectors like healthcare, software development, and service industries, demonstrating its versatility and effectiveness in improving efficiency and customer satisfaction.
Comparing Lean and Kaizen
While Kaizen and Lean methodologies aim for continuous improvement and operational excellence, they have distinct characteristics.
Understanding their similarities and differences is crucial for effectively implementing them in business processes.
Similarities:
- Focus on Continuous Improvement: Both methodologies emphasize ongoing process improvement, aiming for higher efficiency and better quality.
- Waste Reduction: Kaizen and Lean prioritize identifying and eliminating waste (Muda) in processes, though their approaches might vary.
- Employee Involvement: Both philosophies encourage employee participation at all levels, recognizing that those closest to work often have the best improvement insights.
- Customer-Centric Approach: Both methods focus on adding value from a customer’s perspective, ensuring the final product or service meets customer needs and expectations.
- Use of Specific Tools and Techniques: Both methodologies employ various tools and techniques, such as 5S (Sort, Set in order, Shine, Standardize, Sustain) for workplace organization to achieve their goals.
Differences:
- Scope and Pace of Change: Kaizen continually advocates small, incremental changes. Lean, while endorsing continuous improvement, often involves larger, more systemic process changes.
- Origin and Application: Kaizen originated as a broad philosophy encompassing all aspects of a business, while Lean started specifically in manufacturing and production. However, both have since expanded to various sectors.
- Process vs. System Approach: Kaizen focuses more on individual processes and small improvements. In contrast, Lean looks at the entire system to optimize the flow and eliminate waste throughout the value stream.
- Cultural Emphasis: Kaizen emphasizes creating a culture of continuous improvement as part of everyday work, while Lean includes a set of principles and tools aimed at systemic improvements.
- Implementation Strategy: Lean implementation is often project-based, targeting specific areas for improvement, whereas Kaizen encourages ongoing improvement in all areas all the time.
How can businesses integrate both approaches?
When Kaizen meets Lean, businesses can harness a powerful synergy by integrating Kaizen’s culture of continuous, incremental improvements with Lean’s systemic approach to efficiency.
This blend leads to a holistic improvement strategy, focusing on both small daily changes and larger process optimizations, driving sustainable growth and operational excellence.
Conclusion
In conclusion, understanding the nuances between Kaizen and Lean methodologies offers profound insights into business efficiency. While both prioritize continuous improvement and waste reduction, their unique approaches provide complementary strategies for operational excellence.
Integrating these philosophies can create a robust framework for sustainable growth, fostering a culture of perpetual betterment in organizations.
Read more: The Power of Kaizen in Lean Manufacturing