Kaizen, a Japanese term meaning “change for the better,” is a powerful philosophy and action plan that promotes continuous improvement in all aspects of a manufacturing process. By eliminating waste and increasing efficiency, kaizen helps companies achieve lean manufacturing, creating a culture of constant improvement and driving long-term success.
In this blog guide, we will explore the essence of kaizen, its benefits, and how to implement it in your organization effectively.
Understanding Kaizen: A Philosophy And Action Plan
Kaizen is both a philosophy and an action plan.
As a philosophy, it fosters a workplace culture where all employees actively engage in suggesting and implementing improvements. This mindset shift is crucial for the success of kaizen in lean manufacturing. When kaizen becomes a natural way of thinking for upper-level managers and plant-floor employees, it creates a powerful engine for continuous improvement.
As an action plan, kaizen involves organizing events and focus groups that aim to improve specific areas within the organization. These events bring together employees from all levels, emphasizing the insights and expertise of plant-floor workers.
By harnessing the collective talents within a company, kaizen enables regular, incremental improvements that drive efficiency and eliminate waste.
The Benefits Of Kaizen In Lean Manufacturing
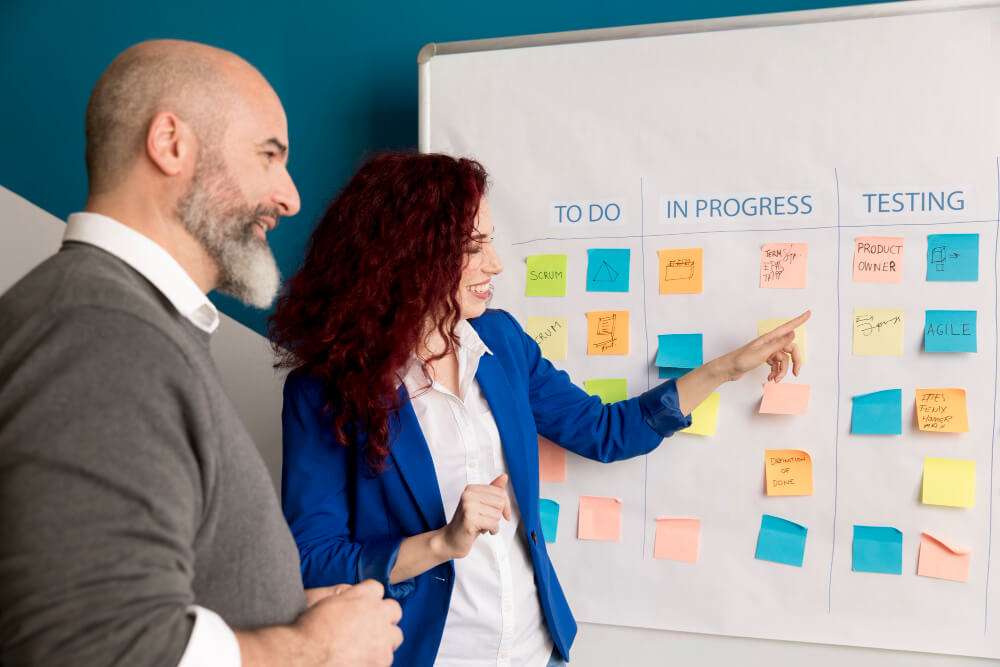
Implementing kaizen in a manufacturing process offers numerous benefits. Take a look at some of the key advantages that make kaizen an essential strategy for lean manufacturing.
1. Waste Reduction And Increased Efficiency
Kaizen identifies and eliminates waste in all forms, including unnecessary motion, transportation, waiting, inventory, defects, and wasted human resources.
Companies can significantly improve efficiency and reduce costs by streamlining processes and minimizing non-value-added activities.
2. Continuous Improvement Culture
Kaizen fosters a culture of continuous improvement by encouraging all employees to participate in suggesting and implementing improvements actively.
This culture shift promotes collaboration, innovation, and learning, creating a dynamic and engaged workforce.
3. Enhanced Quality And Safety
Through kaizen, companies can promptly identify and promptly address quality issues, defects, and safety concerns.
By continuously improving processes, companies can deliver higher-quality products and provide a safer work environment for their employees.
4. Employee Empowerment And Engagement
Kaizen empowers employees by giving them a voice and involving them in decision-making processes.
When employees feel valued and empowered to contribute their ideas and expertise, they become more engaged, leading to increased motivation, productivity, and job satisfaction.
5. Sustainable Long-Term Success
Companies can stay competitive and adapt to changing market demands by embracing kaizen and continuously improving their manufacturing processes.
Kaizen enables companies to remain agile, responsive, and innovative, ensuring sustainable long-term success.
Implementing Kaizen: Key Steps And Strategies
To effectively implement kaizen in your organization, following a structured approach and applying proven strategies is essential. Take a look at the key steps to guide you in your kaizen journey:
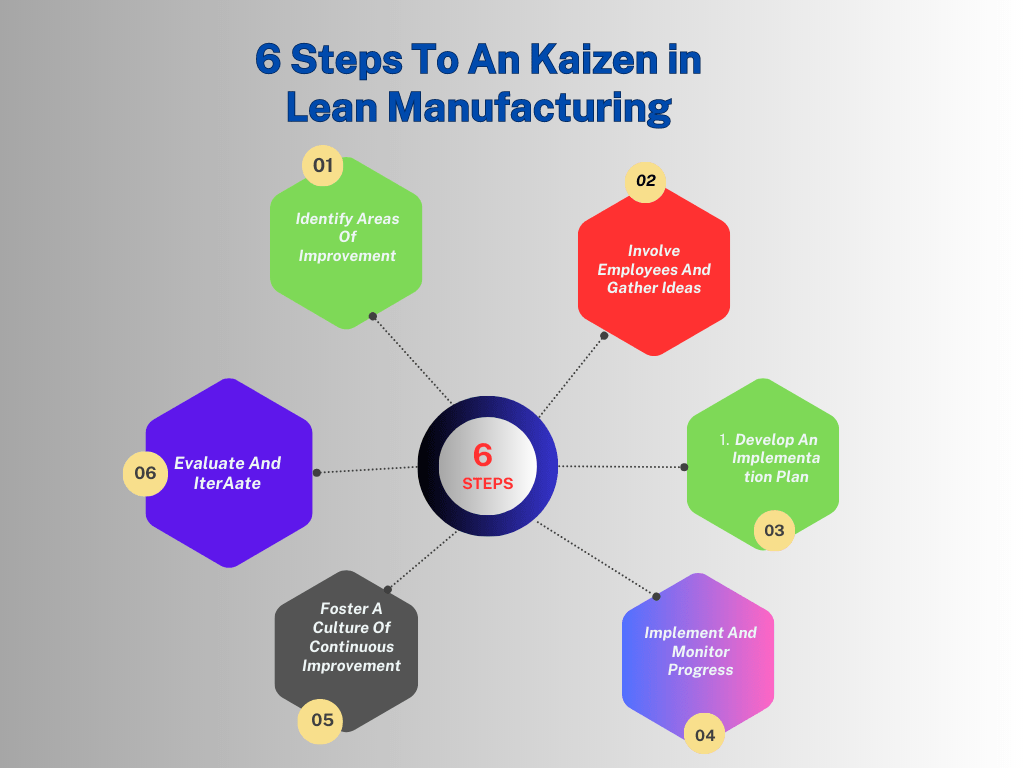
1. Identify Areas Of Improvement
The first step in implementing kaizen is identifying the areas in your manufacturing process that require improvement.
This can be done through observations, data analysis, and conversations with employees at all levels. Look for bottlenecks, inefficiencies, defects, and any areas that can be optimized.
2. Involve Employees And Gather Ideas
Once you have identified the areas for improvement, involve employees from all levels in brainstorming sessions. Encourage them to share their insights, ideas, and suggestions for enhancing the process.
Remember, those directly involved in manufacturing often have valuable knowledge and experience that can drive practical improvements.
3. Develop An Implementation Plan
Based on the ideas and suggestions gathered, develop an implementation plan. This plan should outline each improvement’s specific actions, timelines, and responsibilities.
Consider the resources needed, the training required, and any potential challenges that may arise during implementation.
4. Implement And Monitor Progress
Execute the implementation plan, putting the proposed improvements into action. Monitor the progress regularly and track key metrics to evaluate the effectiveness of the changes.
This data-driven approach enables you to make data-based decisions and make necessary adjustments as needed.
5. Foster A Culture Of Continuous Improvement
To sustain Kaizen’s benefits, fostering a culture of continuous improvement is crucial. Encourage ongoing communication, feedback, and collaboration among employees.
Celebrate successes, recognize contributions, and provide opportunities for further learning and development.
6. Evaluate And Iterate
Regularly evaluate the impact of kaizen on your manufacturing process. Analyze the results, gather employee feedback, and identify areas for further improvement.
Kaizen is an iterative process, and continuous evaluation and iteration are key to its success.
Conclusion
Kaizen is a powerful philosophy and action plan that drives continuous improvement in lean manufacturing. By embracing kaizen, companies can eliminate waste, increase efficiency, enhance quality, and foster a culture of constant improvement.
However, implementing kaizen requires structured steps, employee involvement, and a commitment to ongoing evaluation and iteration. By embracing this philosophy, companies can achieve sustainable long-term success in today’s competitive manufacturing landscape.
Investing in kaizen is investing in the future of your organization. Start your kaizen journey today and unlock the full potential of your manufacturing processes.