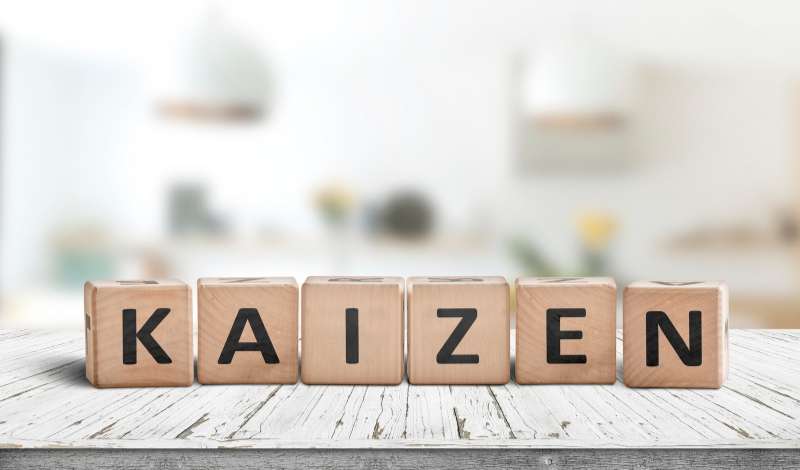
In the search for continuous improvement, businesses across every industry have turned to the powerful tool known as the “Kaizen board.” These visuals help serve as a focal point for teams to track progress, brainstorm ideas, and streamline processes.
In this article, we’ll explore the concept of Kaizen boards and provide practical examples from various sectors, demonstrating how this versatile tool can spark positive change and foster a culture of improvement within your organization.
What is a Kaizen Board?
A Kaizen board is a visual management tool used to facilitate the principles of Kaizen, a Japanese term meaning “continuous improvement.” It typically consists of a physical or digital board divided into sections or columns where teams can track and manage improvement initiatives, ideas, and tasks.
These boards provide a clear overview of ongoing projects, promote communication among team members, and encourage the incremental improvement of processes, products, or services. Kaizen boards are widely used in various industries to promote a culture of continuous improvement and accountability.
Kaizen Board Examples Across Several Industries
Kaizen boards are versatile tools that can be adapted to suit the specific needs of various industries. Here are some examples of how Kaizen boards can be applied:
1. Manufacturing Industry
- Problem-Solving Kaizen Board: Used to identify and address production issues in real-time, such as equipment breakdowns or quality defects, enabling immediate corrective action.
- 5S Kaizen Board: Focuses on sorting, straightening, shining, standardizing, and sustaining workplace organization, leading to increased efficiency and safety.
2. Healthcare Sector
- Patient Flow Kaizen Board: Helps hospitals and clinics optimize patient care processes, reduce waiting times, and enhance patient satisfaction.
- Medication Management Kaizen Board: Ensures efficient medication administration, reducing errors and enhancing patient safety.
3. Software Development
- Agile Kaizen Board: Agile teams use it to manage user stories, prioritize tasks, and track progress in software development projects.
- Bug Tracking Kaizen Board: Tracks and resolves software bugs efficiently to improve software quality.
4. Retail Industry
- Inventory Management Kaizen Board: Aids in monitoring stock levels, identifying slow-moving items, and optimizing the supply chain for better stock turnover.
- Visual Merchandising Kaizen Board: Ensures stores maintain attractive displays and layouts to enhance the shopping experience.
5. Office Environments
- Project Management Kaizen Board: Helps teams manage tasks and projects, fostering collaboration and timely project completion.
- Meeting Improvement Kaizen Board: Focuses on enhancing meeting effectiveness by tracking agenda items, action items, and follow-ups.
Kaizen boards, tailored to specific industries, serve as essential tools for continuous improvement, encouraging teams to identify and implement small, incremental changes that lead to substantial overall enhancements.
How To Implement A Kaizen Board?
Here are the steps to effectively implement Kaizen:
- Update the Kaizen Card: Ensure that the Kaizen Card contains all necessary information, including problems, proposed improvements, start date, expected benefits, required input, and priority level (high, standard, or low).
- Place the Kaizen Card on the Whiteboard: Add the Kaizen Card to the “To Do” section of the whiteboard. On the same day, discuss the improvement idea with your manager and seek approval for its implementation.
- Move to the “Doing” Section: After receiving approval, move the Kaizen Card to the “Doing” section of the whiteboard. Begin working on implementing the improvement.
- Verification by Manager: Once the improvement is in place, ask your manager to review and confirm the results. If the improvement proves successful, your manager should mark it as “Result Verified. YES.”
- Standardization Efforts: If the same improvement can benefit another team or department, contact them and help them prepare their Kaizen Card. Mark the method as standardized within the company.
- Completion and Archive: Finally, add the completion date to the Kaizen Card and move it to the “Done” section on the Kaizen board.
Benefits of Implementing a Kaizen Board in Your Workplace
Implementing a Kaizen board in your workplace can offer numerous benefits, fostering a culture of continuous improvement and driving positive change. Here are some key advantages:
- Enhanced Visibility: Kaizen boards provide a clear, visual representation of ongoing projects, tasks, and improvement initiatives, ensuring that everyone in the organization can easily see progress and updates.
- Increased Accountability: Assigning tasks and responsibilities to the board clarifies who is responsible for what, leading to improved accountability and ownership of outcomes.
- Efficient Problem-Solving: Kaizen boards facilitate identifying and resolving issues in real time, helping teams address problems promptly and preventing them from escalating.
- Improved Communication: By centralizing information on the board, teams can communicate effectively, share ideas, and collaborate on solutions, promoting better teamwork.
- Empowered Employees: Kaizen boards enable employees at all levels to contribute their ideas for improvement, making them feel more engaged and valued in the workplace.
- Data-Driven Decision Making: The data collected on the board helps make informed decisions as trends and patterns become more visible, aiding in resource allocation and prioritization.
- Streamlined Processes: Continuously monitoring and optimizing processes through Kaizen boards increases efficiency and reduces waste, ultimately improving productivity.
- Positive Culture Shift: Kaizen boards encourage a culture of continuous improvement, where employees are more open to change, innovation, and adapting to new challenges.
- Cost Reduction: Kaizen boards can help reduce operational costs by identifying and eliminating inefficiencies and waste.
- Customer Satisfaction: Improved processes and products from Kaizen initiatives often lead to higher customer satisfaction and loyalty.
- Measurable Results: With clear goals and metrics on the board, organizations can measure the impact of their improvement efforts, demonstrating the value of Kaizen.
- Adaptability: Kaizen boards can be customized to fit the specific needs and goals of different organizational departments or teams.
Conclusion
In conclusion, the Kaizen board is a powerful catalyst for continuous improvement across various industries. Its ability to enhance visibility, communication, and accountability fosters a culture of innovation and efficiency. By implementing Kaizen boards, organizations can unlock their full potential, deliver better results, increase employee satisfaction, and sustain growth.
Read more: The Power of Kaizen in Lean Manufacturing