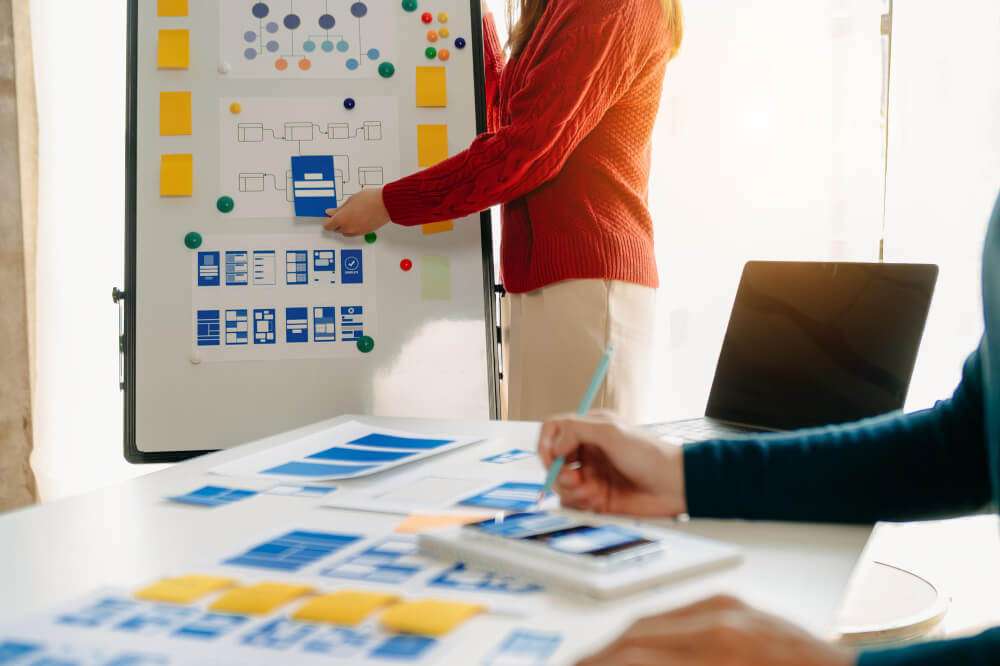
Visual management is an essential strategy for manufacturing and logistics companies aiming to improve their operations and implement best practices. By offering a clear view of processes, work standards, and potential problems, visual management paves the way for streamlined workflows and increased productivity.
In this blog, we’ll delve into the concept of what is visual management, its benefits, and various tools and techniques that can be employed to optimize manufacturing processes and outcomes.
What Is Visual Management?
Visual management is an approach that leverages the power of visual aids to present crucial information about workplace processes. It enforces work standards and highlights or prevents issues.
Rooted in Lean thinking, visual management encompasses a wide range of techniques that aim to make information easily understandable and accessible within the workplace.
The Importance Of Visual Management
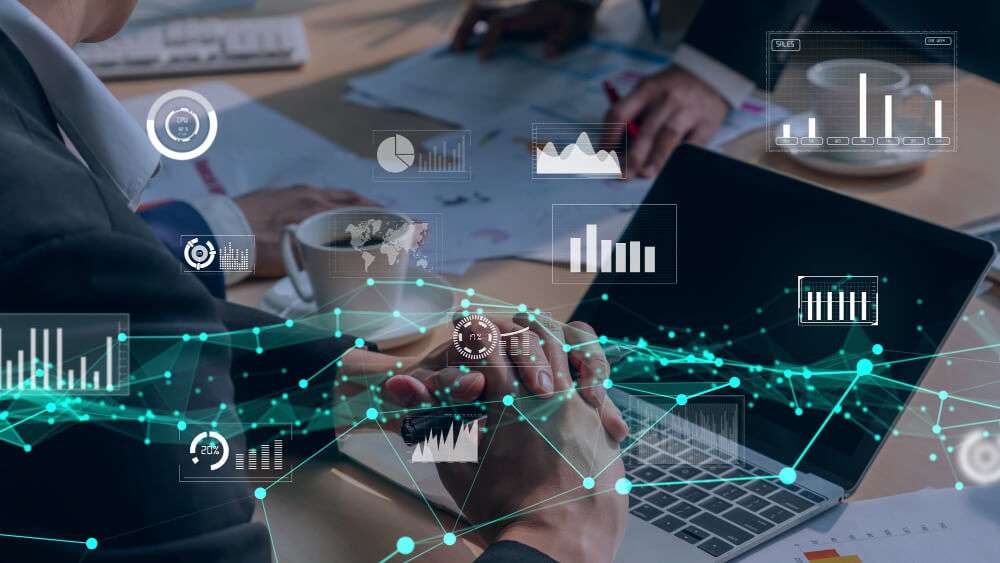
Effective communication is crucial for maintaining smooth and error-free operations in manufacturing facilities. Visual management helps bridge the gap between management and shop floor workers. It ensures everyone is on the same page and working towards their goals.
By providing clear, concise, and easily accessible information, visual management fosters transparency, accountability, and collaboration among team members.
Types Of Visual Management
There are various forms of visual management, each with its unique approach and benefits. Let’s explore each type to understand better “what is visual management” and how they fit within the lean methodology.
1. Factory Layout
Factory layout visual management involves designing and organizing the factory floor to optimize production. The technique employs visual indicators that help the workers to know where everything is located, where they need to go, and what they should do next.
For example, using color codes can signify different zones for various activities. Green could represent assembly, yellow could represent inspection, and red could show where safety equipment is needed. You can also use floor markings to show the path for forklifts and vehicles to move materials and goods around.
Thus, by organizing assembly lines, workstations, and storage areas logically, visual management in factory layouts ensures that employees can easily navigate the facility and understand their role in the production process.
2. Tools and Parts
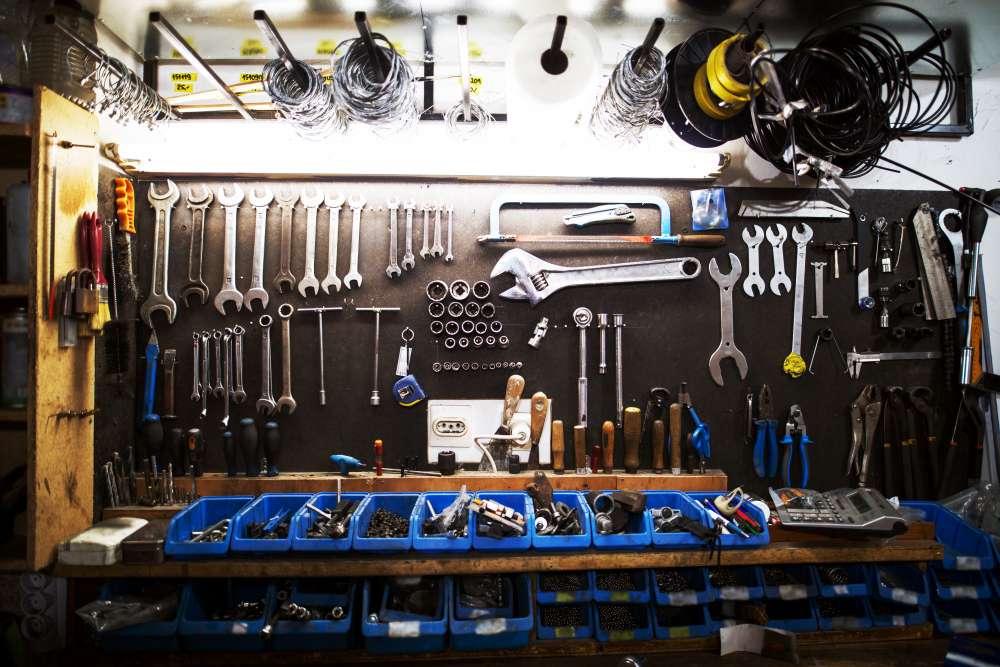
An organized and clean workplace leads to a more productive workforce. Visual management focuses on organizing and managing tools and parts, making it easier for employees to locate and utilize them.
A shadow board or Kaizen foams are often used in this process which utilizes colorful outlines of tools displayed on a pegboard.
This type of visual management puts each tool in its proper place, makes them easier to find, keeps everything clean and organized, and reduces the time spent searching for required equipment.
3. Markings
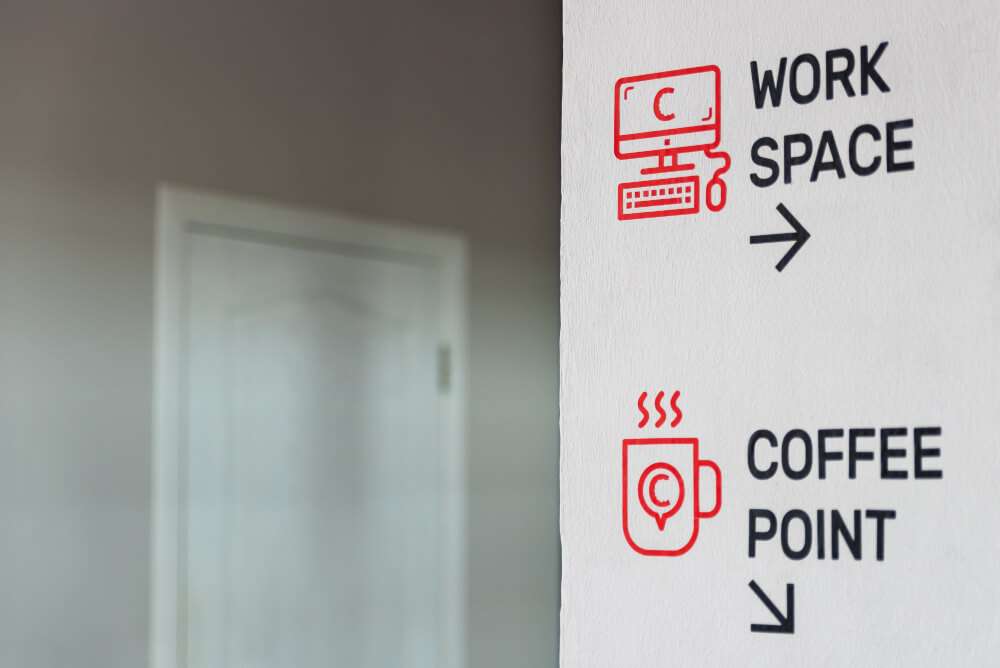
Markings, also known as visual cues, are designs used to attract attention or convey specific information throughout the shop floor. These cues can be shapes, symbols, or words that give a signal or a prompt for people in the workplace.
For example, a green square or check mark placed on a machine could indicate that the machine is operational. Whereas, a red X or circle placed on a machine could suggest that the machine is down or non-operational.
4. Data Displays
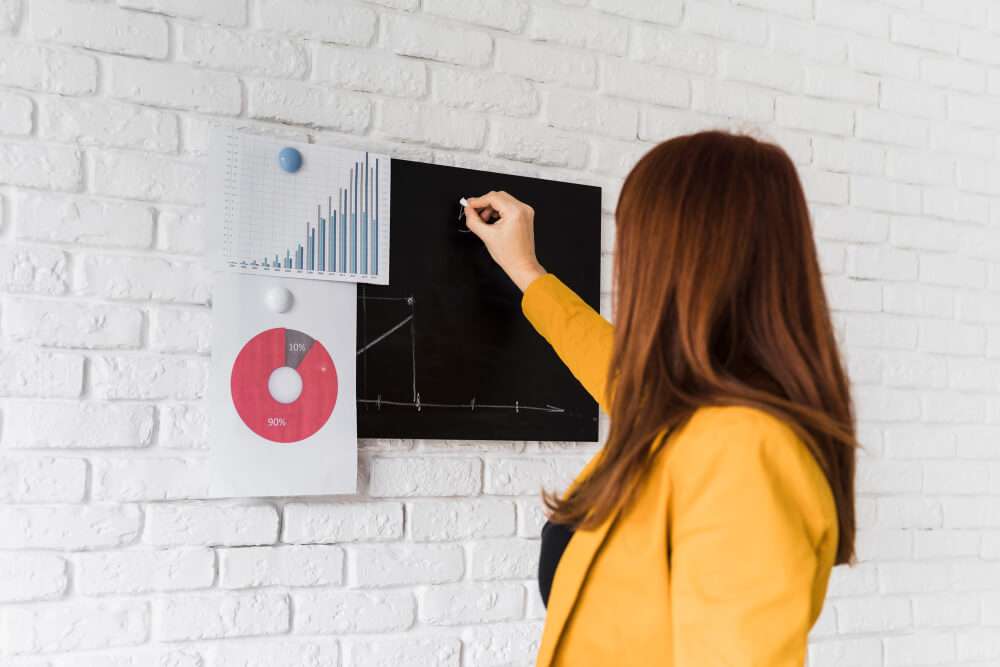
Data displays are visual elements that allow data to be presented in an easily understood manner. A company can use charts, graphs, or diagrams to present data about performance and production.
Employees can access this data in real-time, making it possible to see how they are performing at any given moment.
This type of visual management generates reports and data for managers, providing insight into optimizing the production flow, monitoring performance, and promptly addressing problems.
Primary Functions Of Visual Management
1. Sharing Information
Visual management simplifies the communication of vital information through dashboards, markings, lights, charts, graphs, shadow boards, and other visual aids.
2. Establishing Work Standards
By tracking and displaying work-related data, visual management helps develop work standards to set a baseline pace. It also provides a clear, step-by-step guide for processes.
3. Communicating Work Standards
Once work standards are established, visual management techniques can be utilized to present work standards comprehensively, making it easy for employees to follow them.
4. Identifying Problems
Visual management systems can quickly detect issues, allowing supervisors and workers to address them promptly and focus on other tasks.
5. Solving Problems
Adequate lean manufacturing visual controls can resolve problems by providing clear process instructions, removing confusion, and preventing errors.
Advantages Of Implementing Visual Management
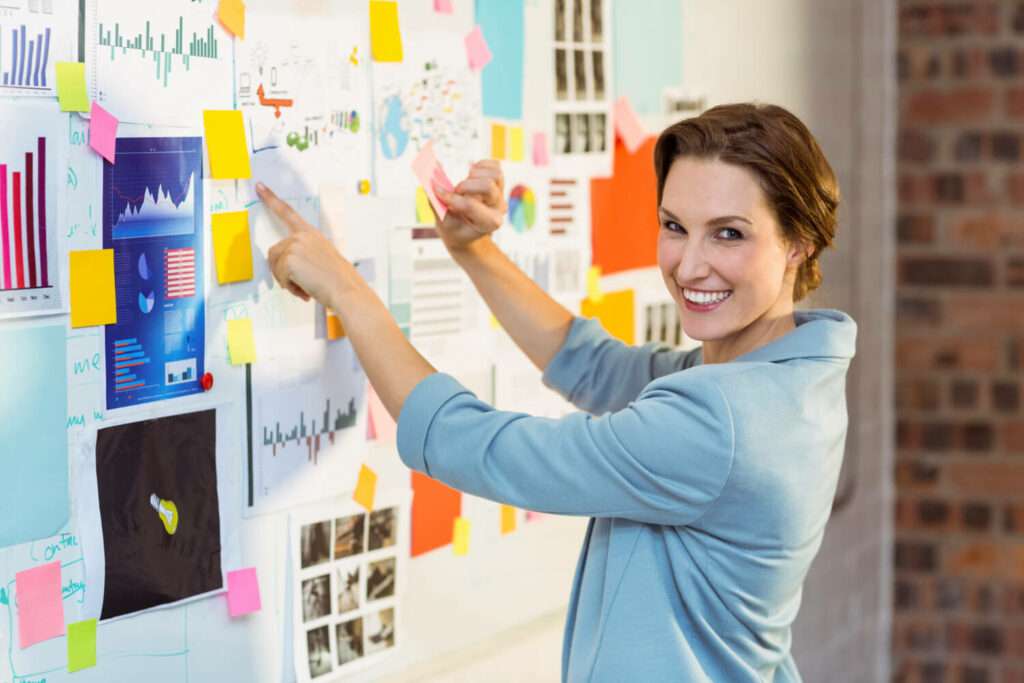
Implementing visual management in lean offers several benefits for employees and the overall business. Take a look at the following:
1. Optimized Inventory
Applying visual management to inventory management can help prevent overstock, stockouts, and extra work among operators searching for inventory.
2. Transparent Processes
Visual management enables a clear view of processes, allowing operators and supervisors to understand the workflow better.
3. Accountability and Consistency
With transparent processes, holding workers accountable for their actions becomes easier, resulting in improved consistency.
4. Facilitating Work
Visual management removes ambiguity, helping operators and supervisors focus on value-added tasks while minimizing interference between tasks.
5. Reduced Training Needs
Visual management can facilitate real-time training by making work processes intuitive and enabling operators with limited experience to learn tasks quickly.
Moreover, Visual management can enhance workplace safety by providing clear instructions and reducing errors.
6. Enhanced Process Efficiency
Clear visual cues and process design using visual management can significantly improve process efficiency by reducing ambiguity and preventing errors.
Besides, Visual management tools can help identify and eliminate waste, a fundamental principle of Lean methodology.
Visual Management Tools Examples
- 5S control boards
- Project status boards
- Kanban cards
- Metrics dashboards
- Andon lights
Conclusion
Visual management gives manufacturing companies effective ways to optimize their processes efficiently. By introducing clarity and visibility into organizations, managers, and workers gain insight into how tasks are performed and what improvements can be made.
Admittedly, implementing such protocols can seem difficult initially, but when done correctly, they offer numerous benefits that impact a company’s performance, safety standards, and customer satisfaction.Thus, visual management is a practical framework for streamlining operations and improving efficiency throughout the manufacturing process: a solution that ensures productivity and success for years to come.