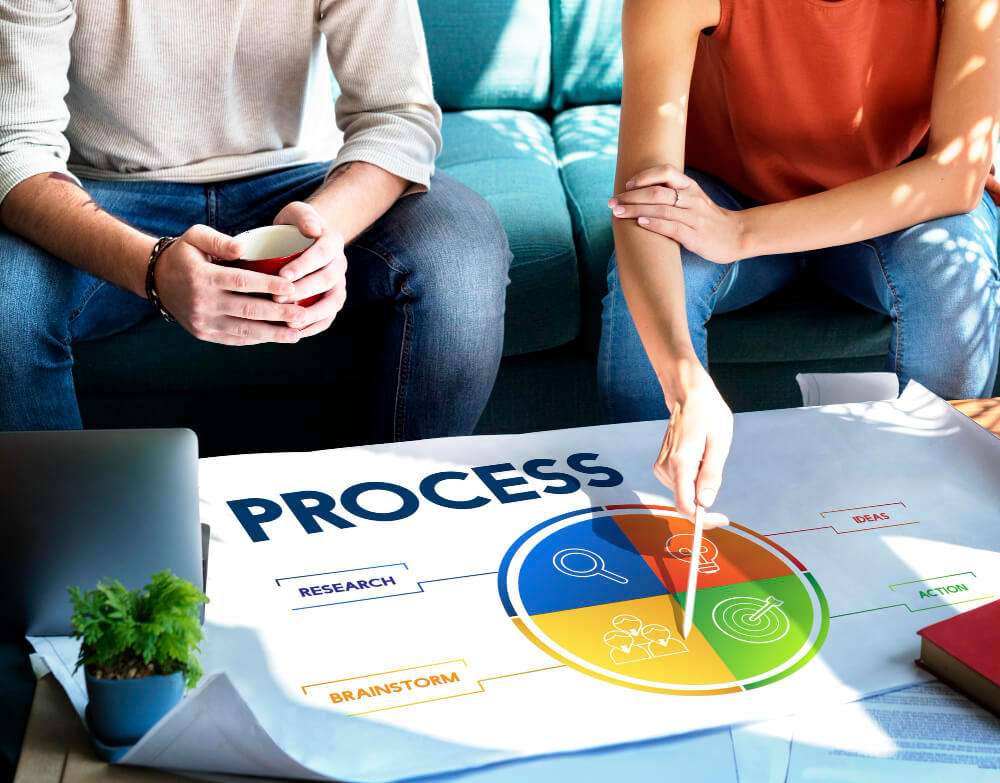
The 5S process is a powerful lean management tool. It has transformed countless organizations by streamlining their operations, improving productivity, and fostering a culture of continuous improvement.
Originating in Japan, this method has gained global recognition for its effectiveness in manufacturing and office environments. In this article, we will explore the key benefits of 5s process implementation in your organization and how it can help you achieve greater success.
What Is 5s?
5S is an acronym that stands for:
- Sort
- Set in order
- Shine
- Standardize
- Sustain
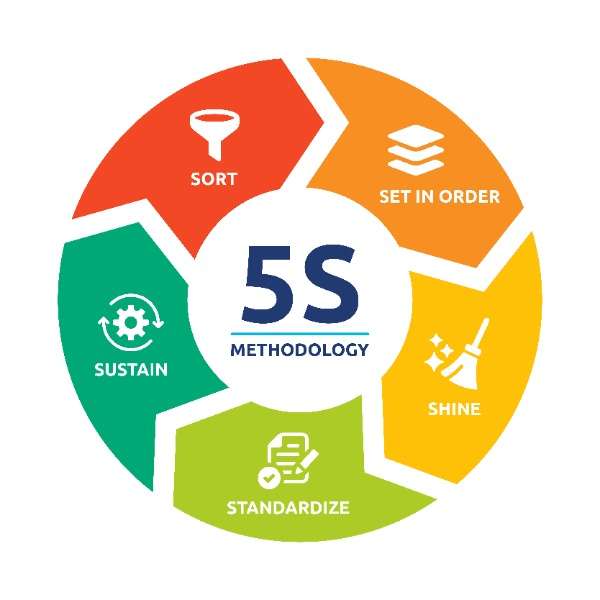
The 5S process can be applied to any workspace, from manufacturing facilities to office environments, and is adaptable to small and large companies. When implemented effectively, these five steps lead to a clean, organized, and efficient workplace. Take a look at how it works:
Benefits Of 5S Implementation
Now that we better understand the 5S process, let’s dive into the benefits of 5s:
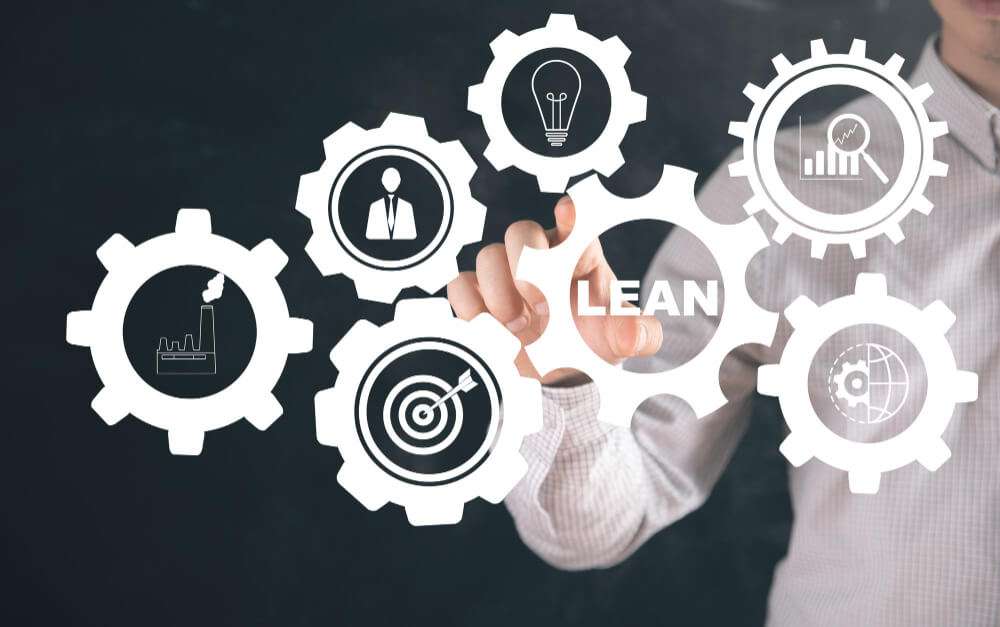
1. Increased Productivity
One of the primary goals of any organization is to improve productivity, which leads to increased revenue and profitability. The benefits of 5s process significantly boost productivity by reducing the time spent searching for tools, materials, and equipment.
By decluttering the workspace and implementing efficient organization systems, employees can work more effectively and complete tasks in less time.
2. Improved Safety
A clean and organized workspace is more pleasant to work in and improves employee safety. Cluttered workspaces can lead to accidents, injuries, and increased exposure to hazardous substances.
By implementing the 5S process, you can reduce the risk of accidents by ensuring that all items are stored in their proper place. You can also see workspace is regularly cleaned and maintained.
3. Enhanced Communication
A key component of the 5S process is using visual cues, such as labels and signs, to communicate important information about the organization and storage of tools and materials.
By implementing a clear and consistent visual communication system, you can reduce confusion and misunderstandings among your team. This will create effective collaboration and teamwork.
4. Enhanced Efficiency
The 5S process is designed to identify and eliminate bottlenecks in the workplace, leading to smoother workflows and more efficient use of resources.
By reducing clutter, improving organization, and streamlining processes, the 5S system can help your organization operate more efficiently. It will enhance the quality of your products or services and reduce production costs.
5. Reduction Of Waste
Through the sorting and organizing stages of the 5S process, organizations can reduce waste by identifying and eliminating unnecessary items. This will free up valuable storage space and minimize the risk of lost or damaged tools and equipment.
In addition, a well-organized workspace can help to reduce waste in the production process by
- Ensuring materials are used efficiently
- Damaged or faulty items are quickly identified and replaced
6. Worker Commitment
Involving employees in implementing the 5S process can increase commitment and engagement. By allowing workers to contribute to improving their workspace, you can foster a sense of ownership and responsibility among your team.
This can lead to higher levels of job satisfaction, lower absenteeism, and improved overall performance.
7. Expanded Storage Space
A cluttered workspace can give the impression of limited storage space, even when ample room is available. Implementing 5s and removing unnecessary items can create more storage space for essential tools and materials.
This will lead to a more organized and efficient workspace. Also, it reduces the need for additional storage solutions or expansions.
8. Streamlined Operations
Implementing the 5S process can streamline your organization’s operations and improve efficiency.
Through the systematic approach to sorting, organizing, and cleaning, you can identify areas of waste or inefficiency and make the necessary changes to improve performance.
As a result, you will see more efficient workflows, faster response times, and improved overall productivity.
9. Fostering A Culture Of Continuous Improvement
One of the most significant benefits of the 5S process is the way it fosters a culture of continuous improvement within your organization.
By constantly evaluating and refining your processes, you can ensure that your workplace remains adaptable and responsive to changing circumstances – and always strives for improvement.
Conclusion
Implementing the 5S process in your organization can bring numerous benefits, from increased productivity and safety to improved efficiency and quality control. By following the 5s steps, you can create a clean, organized, and efficient workspace that contributes to your organization’s success and fosters a culture of continuous improvement. If you want to transform your organization and unlock its full potential, consider embracing the 5S process and experiencing the benefits for yourself.