Beyond the Basics: 5 Next-Level 5S Improvement Ideas for Success
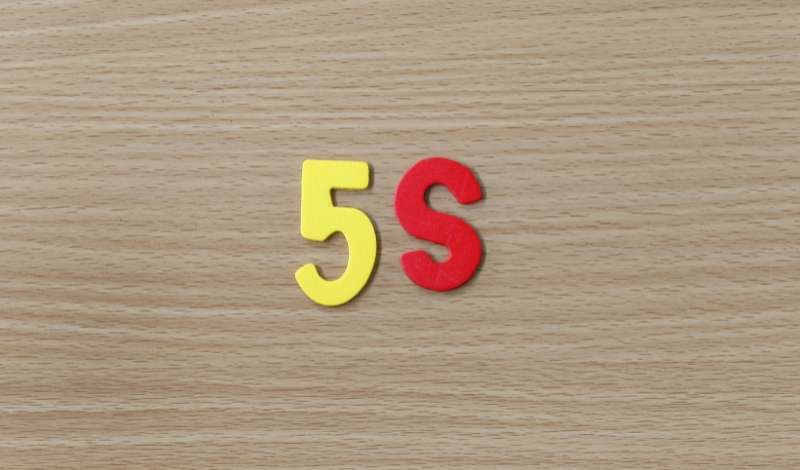
At the core of the 5S methodology is a philosophy and culture that drives its effectiveness. Your company’s willingness to fully adopt and integrate its principles is crucial to the success of the process. When implemented correctly, a 5S system brings numerous benefits, including reduced costs, enhanced quality, heightened safety, increased productivity, and greater employee […]
The Food Retail Guide to Better Hygiene: Protecting Food and Profits
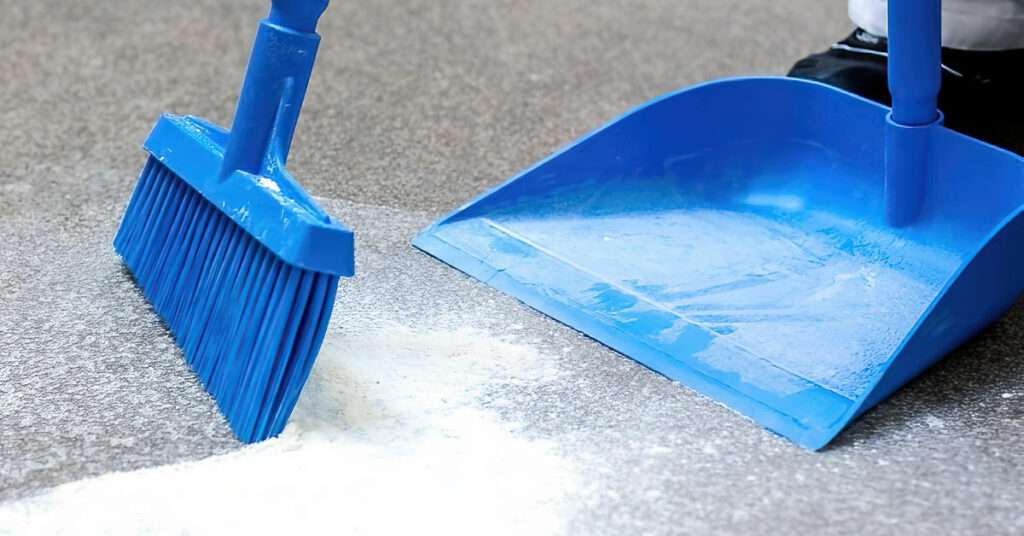
Avoiding food contamination incidents is a continuous challenge in food retail outlets like grocery stores and supermarkets. Proper cleaning and sanitation, hygiene, and material handling practices must be implemented to mitigate these risks. Equally as important, the selection, cleaning, storage, care, and maintenance of tools and equipment also need to be emphasized. There is no […]
Why Are 5s And Color-Coding Important In The Food Industry?
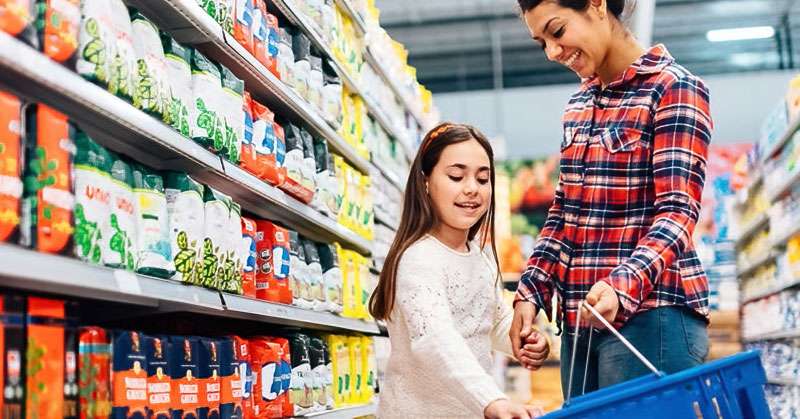
In the food industry, it is imperative to maintain high levels of cleanliness and organization to ensure the safety of consumers. This is where the 5s in the food industry comes in handy. The 5S approach entails sorting, straightening, shining, standardizing, and sustaining. By implementing this methodology, workers in the food industry can quickly locate the […]
Deep Cleaning Protocols After a Food Manufacturing Facility Shutdown
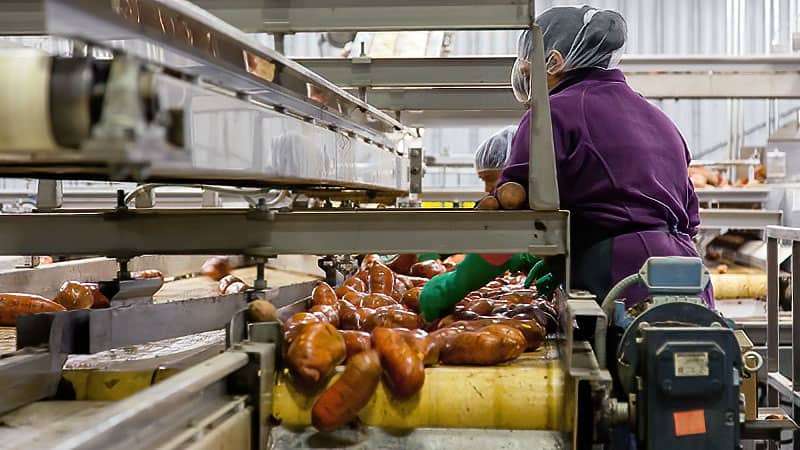
Deep Cleaning Protocols After a Food Manufacturing Facility Shutdown The ongoing COVID-19 pandemic is disrupting normal operations for countless food and beverage manufacturers. This disruption may occur due to limited staff numbers (as a result of social distancing requirements, layoffs, or staff sickness); additional cleaning and sanitation requirements in relation to the control of COVID-19 […]
Lean Vs Automation
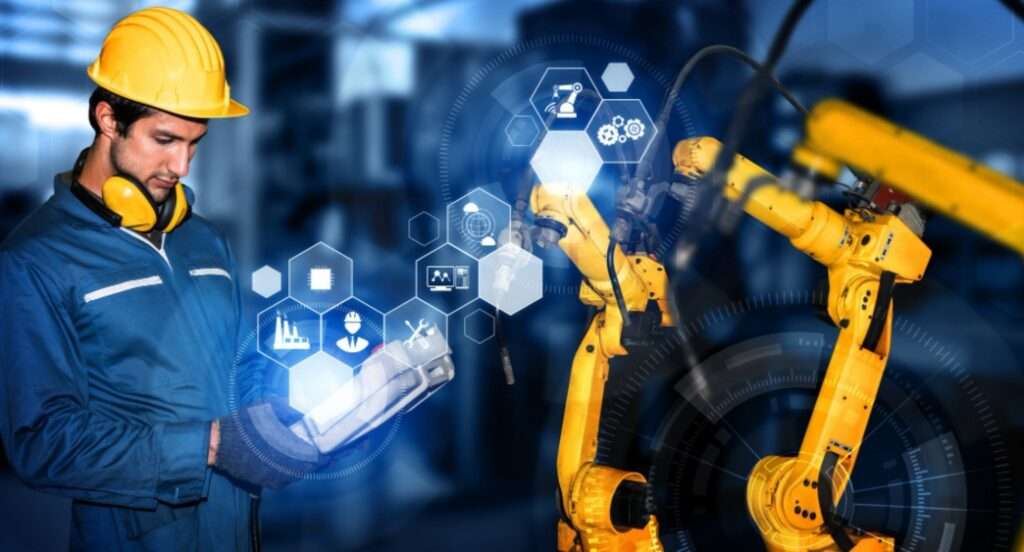
An important question to consider when going lean. Experts discuss top considerations for making new equipment and lean initiatives work together.
Traditional Pegboards vs Printed Shadow boards? Who wins? You decide.
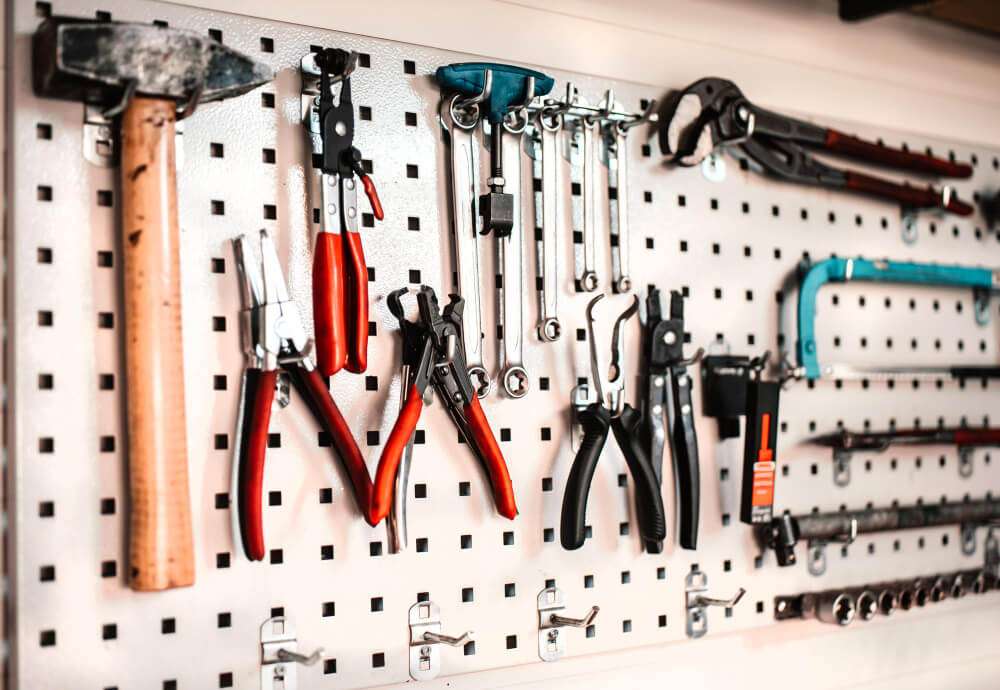
Shadow boards and peg boards are frequently used both personally and professionally. They help to keep the workplace organised and all of your tools together so that you can locate them easily.