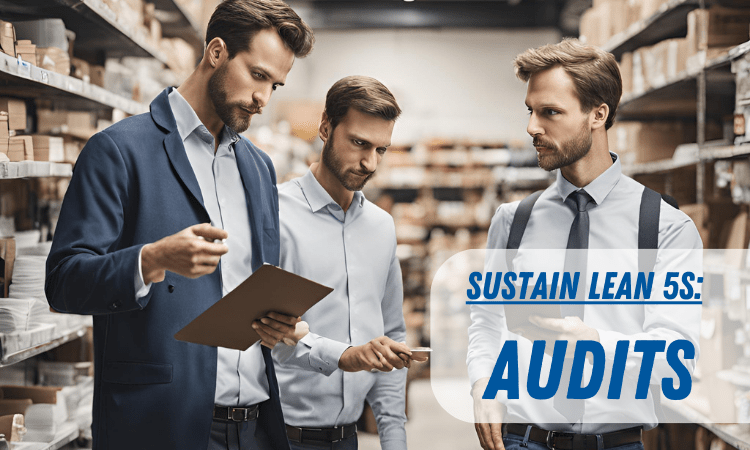
Sustaining a Lean 5S system is more than a one-time event, it is an ongoing process, starting with regular 5S Audits.
Conduct Regular Lean 5S Internal Audits
Internal 5S audits are essential for ensuring the long-term success of Lean 5S initiatives. They provide valuable feedback, drive continuous improvement, and help to create a safe, efficient, and productive work environment.
- Sustaining 5S Improvements:
- Internal 5S Audits are the primary mechanism to ensure that the initial improvements achieved through 5S implementation are maintained over time. Without regular checks, workplaces can gradually revert to their previous disorganized state
- Identifying Areas for Improvement: Audits uncover areas where 5S standards are not being met. This could include:
- Hidden waste: Unnecessary items, disorganized storage, and inefficient workflows.
- Safety hazards: Clutter, spills, and poorly maintained equipment.
- Quality issues: Contamination, errors, and rework caused by a disorganized environment.
- Reinforcing 5S Principles:
- Regular audits reinforce the importance of 5S principles among employees. They serve as a constant reminder that 5S is not just a one-time event, but an ongoing commitment.
- Driving Continuous Improvement:
- Audit findings provide valuable data for continuous improvement. By analyzing trends and identifying root causes of non-conformances, organizations can make targeted improvements to their 5S practices.
- Improving Employee Morale:
- A well-maintained workplace can significantly boost employee morale. Audits help to create a culture of order, cleanliness, and efficiency, which can improve employee satisfaction and engagement.
- Demonstrating Commitment:
- Conducting regular 5S audits demonstrates a commitment to workplace excellence and a focus on continuous improvement to stakeholders, including customers, suppliers, and investors.
8 Steps to build your Lean 5S Audit System:
- Define Audit Scope:
- Areas: Specify the areas to be audited (e.g., workstations, common areas, offices).
- Frequency: Determine the audit frequency (e.g., daily, weekly, monthly).
- Team: Select a team of auditors (e.g., supervisors, team leaders, employees).
- Develop an Audit Checklist:
- Sort:
- Are unnecessary items removed?
- Is there a clear distinction between necessary and unnecessary items?
- Set in Order:
- Are items stored in designated locations?
- Are locations clearly marked and easily accessible?
- Is everything in its place?
- Shine:
- Is the workplace clean and free of debris?
- Are equipment and tools clean and well-maintained?
- Are spills cleaned up promptly?
- Standardize:
- Are 5S standards documented and communicated?
- Are visual controls (e.g., shadow boards, color-coding) used effectively?
- Are standard work instructions followed consistently?
- Sustain:
- Are 5S practices integrated into daily work routines?
- Are employees actively involved in maintaining 5S?
- Are 5S improvements recognized and rewarded?
- Sort:
- Conduct the Audit:
- Observe: Observe the workplace and employee behavior.
- Interview: Interview employees about their 5S practices.
- Document: Record audit findings and observations.
- Take Photos: Document the current state of the workplace.
- Analyze Audit Findings:
- Identify areas of strength and weakness.
- Determine root causes of non-conformances.
- Prioritize areas for improvement.
- Develop Corrective Action Plans:
- Create action plans to address identified issues.
- Assign responsibility for implementing corrective actions.
- Set deadlines for completion of corrective actions.
- Implement Corrective Actions:
- Monitor the implementation of corrective actions.
- Ensure that corrective actions are effective and sustainable.
- Communicate Results:
- Share audit findings and corrective action plans with employees.
- Recognize and reward teams and individuals for 5S achievements.
- Use audit data to track progress and identify trends.
- Continuous Improvement:
- Regularly review and update the audit process.
- Incorporate employee feedback to improve the audit process.
- Continuously refine 5S standards and practices.
Tips for Successful 5S Sustainment Audits:
- Involve Employees: Encourage employee participation in all stages of the audit process.
- Focus on Improvement: Emphasize continuous improvement rather than punishment.
- Use Visual Aids: Utilize visual aids such as scorecards, charts, and photos to communicate audit results.
- Celebrate Success: Recognize and reward teams and individuals for their 5S efforts.
- Make it Fun: Incorporate gamification elements to make audits more engaging.
By implementing a robust 5S audit process, organizations can ensure the long-term sustainability of their 5S initiatives and reap the full benefits of a lean and efficient workplace.