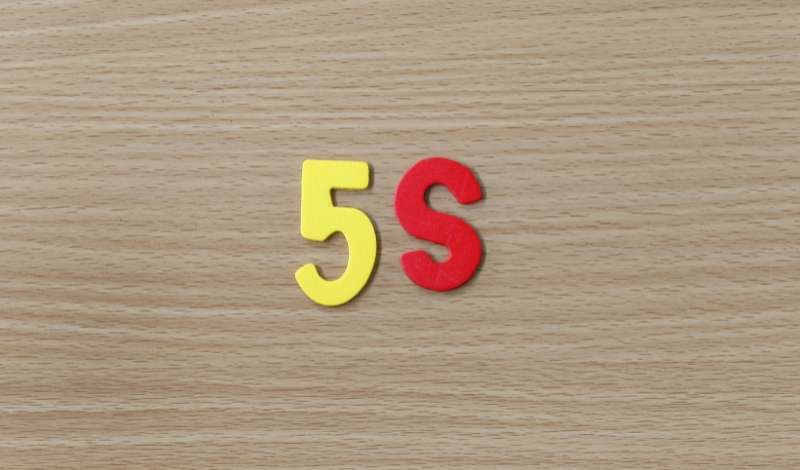
At the core of the 5S methodology is a philosophy and culture that drives its effectiveness. Your company’s willingness to fully adopt and integrate its principles is crucial to the success of the process. When implemented correctly, a 5S system brings numerous benefits, including reduced costs, enhanced quality, heightened safety, increased productivity, and greater employee satisfaction.
Although the framework of 5S is straightforward and uncomplicated, many organizations still struggle to implement it effectively. To assist in establishing a successful 5S system and pave the way for a more organized and efficient workplace, consider these 5S improvement ideas in the article below.
The 5s Methodology
Originating from Toyota in the 1960s, the 5S methodology was developed for industrial settings to create more organized, neater, and cleaner workspaces to enhance productivity and foster a better working environment.
This methodology has gained global recognition, with numerous companies and organizations adopting it worldwide. Despite its conceptual simplicity and the lack of need for intricate training or highly specialized expertise, implementing the 5S methodology demands strict discipline and a systematic approach.
5s Examples In Daily Life
The 5S methodology, though rooted in industrial environments, can be effectively applied in everyday life to organize spaces and streamline daily routines. Here are some examples:
- Sort (Seiri): Decluttering your home by removing unnecessary items.
- Set in Order (Seiton): Organizing your workspace so everything has a specific place.
- Shine (Seiso): Regularly clean your living areas, like sweeping and dusting.
- Standardize (Seiketsu): Establishing routines for household chores to maintain cleanliness and order.
- Sustain (Shitsuke): Consistently follows these practices to keep spaces organized and efficient.
5s Improvement Ideas
Here are ten 5s improvement ideas for achieving success at your workplace. These strategies are integral 5S improvement ideas aimed at enhancing the system’s effectiveness and fostering a culture of organization and efficiency.
1: Begin with a Focused Approach
For effective 5S system implementation, identify specific areas or zones to apply the principles. Choose these based on cost, necessity, risk, and safety. Demonstrating success in a particular part of the organization can encourage wider acceptance and lay a solid groundwork for a sustainable 5S system.
2: Ensure Availability of Necessary Tools
Employees must easily access the right tools and supplies to maintain an effective 5S system. If employees need help finding required items, they may lose interest in the system while wasting time searching. Here’s a list of essential supplies to keep readily available:
- Labeling tools like label makers and various types of labels
- Different kinds of tapes, including floor tape and marking tape
- Various tags like red tags and 5S tags
- Educational and training materials
- Organizational tools like tool shadows, shadow boards
- Cleaning charts and cleaning supplies
- A dedicated 5S cart stocked with necessary items
- A camera for documentation
- Various bins, holders, and organizers for efficient storage
3: Prioritize Comprehensive Training
Practical training is critical to the success of a 5S system. With adequate training and tools, employee engagement in the system can continue. Utilize various methods like classroom sessions, instructional videos, 5S workshops, and reading materials to provide thorough initial training and ensure the successful launch of your 5S system.
4: Utilize Visual Demonstrations
Since most individuals are visual learners, it’s more effective to show rather than just tell what an ideal, organized workspace looks like. Use visual aids like before-and-after photos to illustrate the desired cleanliness and organization.
Displaying ‘before’ pictures near the workspace can help employees visually appreciate progress and track improvements.
5: Set an Example
For a 5S system to be embraced, management must lead by example. A cluttered manager’s office can undermine the system’s credibility. Management should maintain the company’s most organized and cleanest workspaces, setting a standard for others to follow.
This leadership approach is likely to inspire cooperation among staff. Leaders must be well-versed in 5S principles and ready to address and resolve any issues.
6: Define Expectations Clearly
Having well-defined roles for each employee within the 5S framework is essential. These responsibilities should be explicitly outlined in job descriptions.
Regularly underscore the significance of these tasks and their impact on the company’s success. Leaders should be equipped to offer positive and constructive feedback regarding fulfilling these expectations.
7: Integrate, Don’t Segregate
A common mistake is treating the 5S initiative as separate rather than integrating it into the company’s overall improvement strategy. This isolation can lead to confusion among employees about the system’s relevance.
Weave the 5S process into the company’s broader objectives to demonstrate its value. Form review teams and include 5S discussions in leadership and team meetings, focusing on continuous improvement and providing valuable insights for enhancement.
8: Emphasize Daily Compliance
For 5S principles to take root, supervisors, and managers should be vigilant about identifying and addressing any 5S infractions in real time. While regular audits are crucial, daily reinforcement is equally essential for the success of the 5S system.
Ignoring a 5S violation undermines the system’s progress and sends a message that non-compliance is acceptable, potentially leading to increased such violations. Leadership must proactively point out any discrepancies they observe during their interactions on the work floor.
9: Recognize and Celebrate Achievements
Acknowledging and rewarding staff or teams that exceed expectations in the 5S system is necessary. This isn’t about rewarding essential job performance but highlighting those who surpass the set standards.
When conducting monthly inspections, focus on celebrating the highest achievers, as emphasizing the lowest performers can be counterproductive. Before-and-after pictures can effectively showcase examples of exceptional commitment and serve as inspiration for others.
10: Regular Audits for Accountability
Depending on the scope of the area or zone, carry out annual or bi-annual audits to encourage consistent adherence and progress in the 5S system. These audits highlight areas needing attention and set clear expectations for ongoing improvement.
Provide prompt feedback from these evaluations, using the results to motivate and guide further enhancements in 5S practices.
Conclusion
These recommendations are drafted to assist in effectively implementing and maintaining a sustainable 5S system. As you engage in reviews or conduct audits and seek avenues for enhancing your system, revisit these steps to identify potential areas for refinement.
Remember that the 5S system is a continuous journey, not a one-time event. It’s structured to foster ongoing improvement, contributing to the long-term success of your organization. Embrace this philosophy of perpetual progress to realize the full benefits of the 5S methodology.
Read more: What Are The Best 10 Lean Tools? Understand Their Benefits