In any workplace, safety should always be a top priority. One crucial aspect of maintaining a safe working environment is effective communication. Safety tags convey essential information about hazardous conditions, equipment, and operations to employees.
These tags serve as warning signs and reminders, helping to prevent accidents and injuries. This article will explore the different types of safety tags and their significance in ensuring workplace safety.
Inspection Tags
Regular equipment inspections are essential for reducing the chances of equipment failure and worker injury. Inspection tags are crucial in keeping track of inspections and ensuring that equipment is in good working condition.
These tags provide information about the date of inspection, the condition of the equipment, and the name of the person who conducted the inspection.
Specific equipment, such as fire extinguishers, require annual maintenance inspections, while others, like forklifts, need daily checks.
By using inspection tags, employers can easily track when the equipment was inspected and by whom, ensuring compliance with safety regulations and promoting a safe working environment.
Lockout/Do Not Operate Tags
One of the most critical types of safety tags is the lockout/do not operate tag. These tags are essential to OSHA’s safety measures to regulate energy during equipment servicing or maintenance.
They indicate that a machine is currently being serviced and should not be turned on. By using lockout tags, employers can prevent unexpected starting of equipment, which could result in severe injuries.
Lockout/tagout violations were one of the most commonly cited violations by OSHA in 2019. The penalties for such violations can be substantial, reaching up to $13,260 per violation. Implementing these tags helps companies comply with safety regulations and avoid hefty fines.
Ladder & Scaffold Tags
Falls from ladders and scaffolding are a common cause of workplace injuries. To mitigate the risk associated with these accidents, ladder and scaffold tags are crucial.
These tags provide essential information about the inspection status of ladders and scaffolding, indicating whether they are safe to use or if they require maintenance.
In 2019, OSHA cited ladder and scaffold violations as some of the most common violations. Violations of ladder and scaffold safety regulations can result in fines of up to $13,000.
By using a ladder and scaffold tags, employers can improve communication and reduce the chances of improper use, minimizing the risk of accidents and avoiding costly fines.
Machine Tags
Machines are integral to many businesses but can pose significant risks if not properly maintained or operated. Machine tags indicate potentially dangerous equipment, document machine inspections, or identify machinery that is out of service or should not be used.
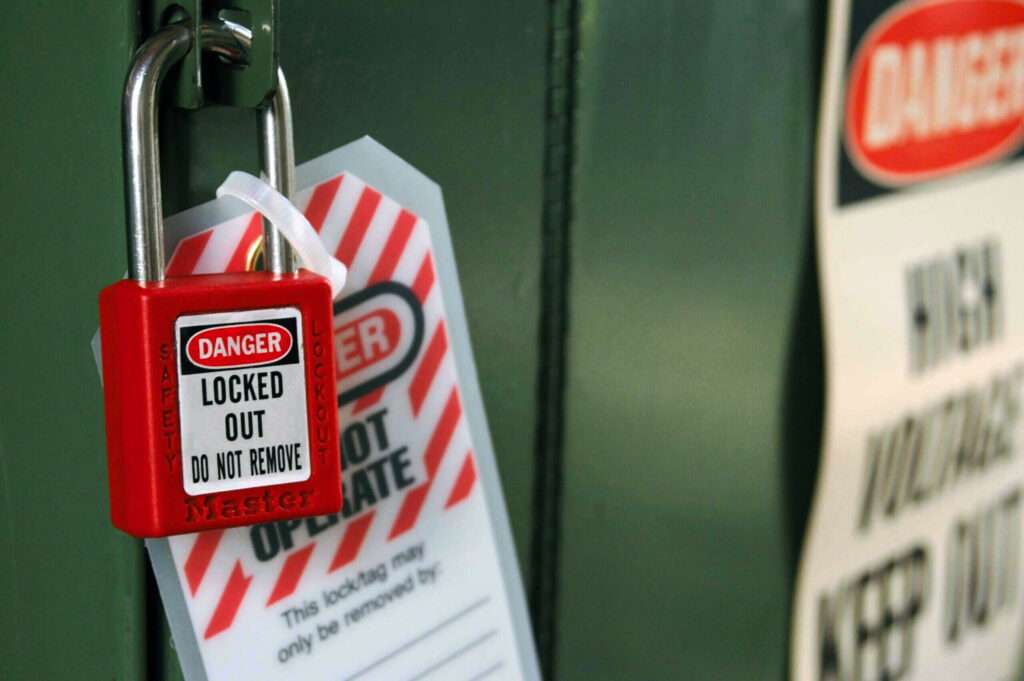
Without the proper tag, a worker may unknowingly use a faulty machine, leading to injuries. By using machine tags, employers can effectively communicate the status of machinery and prevent accidents caused by operating unsafe equipment.
Barricade Tags
Barricades are used to restrict access to regulated areas in the workplace. Barricade tags provide additional information about the barricade, including the reason for its installation, authorized personnel permitted to enter, and the responsible person in charge of the barricade.
Employers can communicate critical information regarding risks, access permissions, and installation and removal timeframes using barricade tags.
These tags help ensure that employees understand the purpose of the barricade and adhere to safety protocols, reducing the chances of accidents or unauthorized access.
Confined Space Tags
Confined spaces pose additional dangers due to limited access and potential hazards. Confined space tags identify restricted, dangerous locations that require permits to enter.
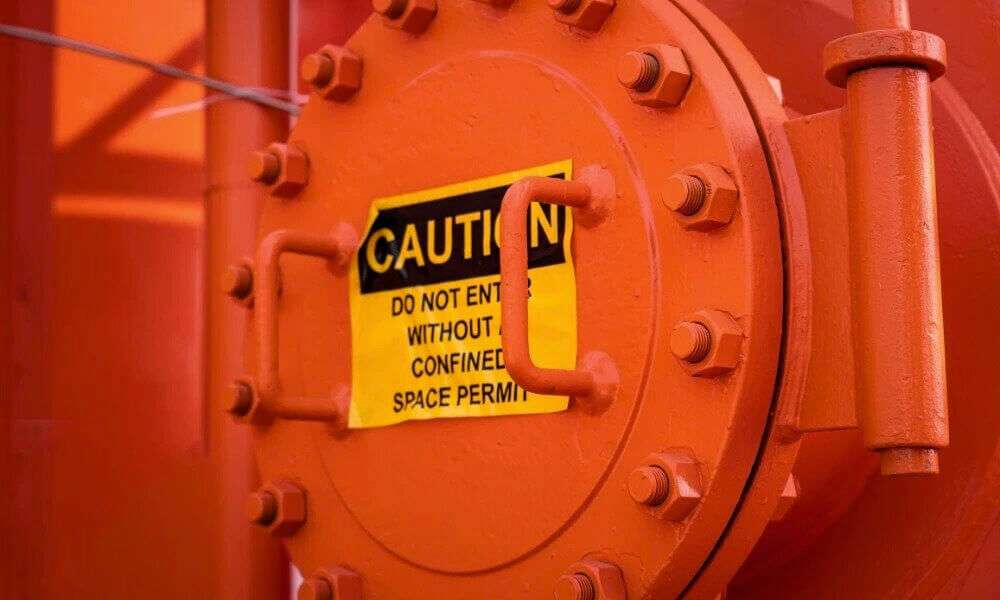
These tags communicate important information about entrance permissions, personnel in confined spaces, inspections, and occupants. Confined spaces that meet specific criteria, such as hazardous atmospheres or the potential for entrapment, must be identified by employers.
Moreover, confined space tags help mark these areas as “permit-required” workspaces, ensuring that employees are aware of the hazards and take necessary precautions when entering such spaces.
Conclusion
Safety tags play a critical role in maintaining a safe working environment. From lockout/do not operate tags to confined space tags, each type specifically communicates hazards and ensures employee safety. By using these tags, employers can comply with safety regulations, prevent accidents, and protect their workers from potential harm. Implementing an effective safety tag system is an essential component of any comprehensive workplace safety program.
Remember, safety tags should always be used in accordance with government regulations, industry standards, and specific requirements for each business/activity.