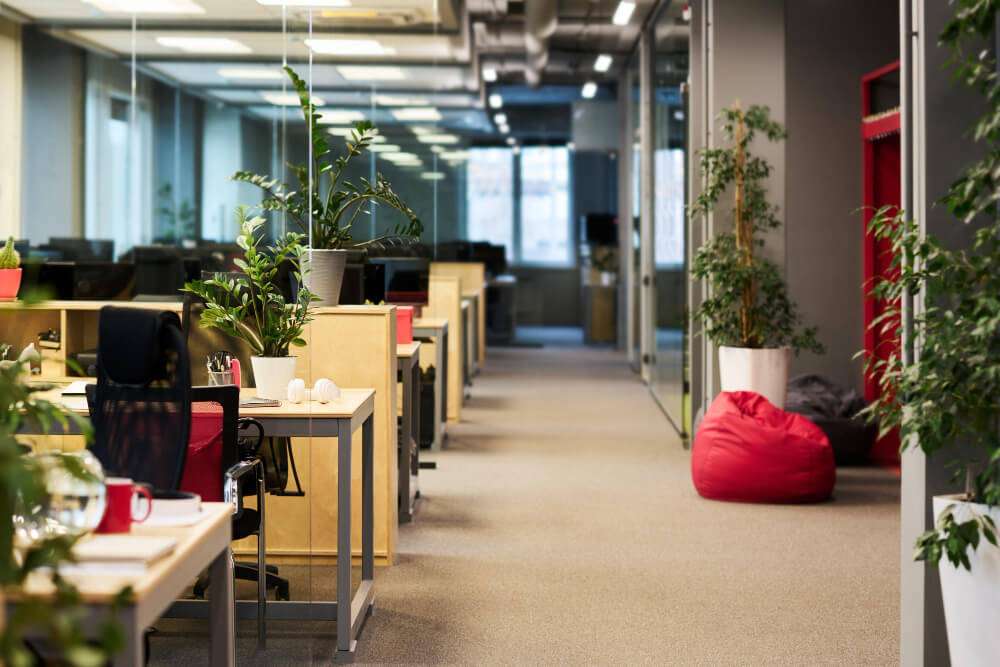
Creating and maintaining a safe workplace is essential for your employees’ well-being and your business’s overall success. A safe work environment promotes employee productivity, reduces the risk of accidents and injuries, and helps you comply with legal requirements.
This comprehensive guide will explore six crucial steps to creating and maintaining a safe workplace and numerous tips and best practices to ensure workplace safety. So, let’s dive into the world of secure workplace promotion!
1. Establish A Strong Safety Culture
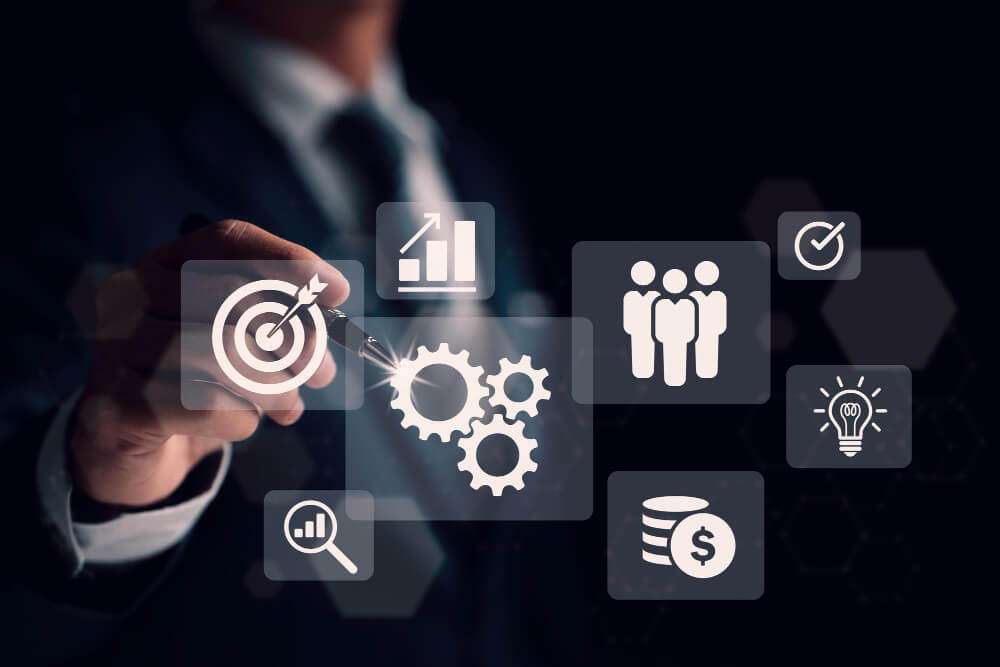
The foundation of a safe workplace is a strong safety culture. This begins with developing a comprehensive safety policy that outlines your company’s commitment to workplace safety.
Your safety policy should include clear goals and objectives—besides the roles and responsibilities of all employees in promoting a safe work environment.
Engage Employees In Safety Efforts
Getting employees involved in safety efforts is crucial for fostering a safety culture. Encourage employees to participate in safety committees or task forces. Also, provide them opportunities to contribute ideas and suggestions for improving workplace safety.
Related Article: 5 Key Benefits of a Clean, Organized Workplace
Empowering employees to take ownership of workplace safety creates a sense of shared responsibility and commitment to maintaining a safe work environment.
Provide Regular Safety Training
Regular safety training ensures all employees know potential hazards and how to respond in an emergency. Training should cover emergency procedures, hazard identification, and proper personal protective equipment (PPE) use.
Besides, regularly update and refresh training materials to inform employees about new safety procedures and best practices.
Recognize and Reward Safe Behavior
Celebrating safety successes encourages employees to prioritize safety in their daily work activities.
Offer incentives, awards, or other forms of recognition for employees who consistently follow safety procedures or contribute to workplace safety improvements.
2. Identify And Assess Workplace Hazards
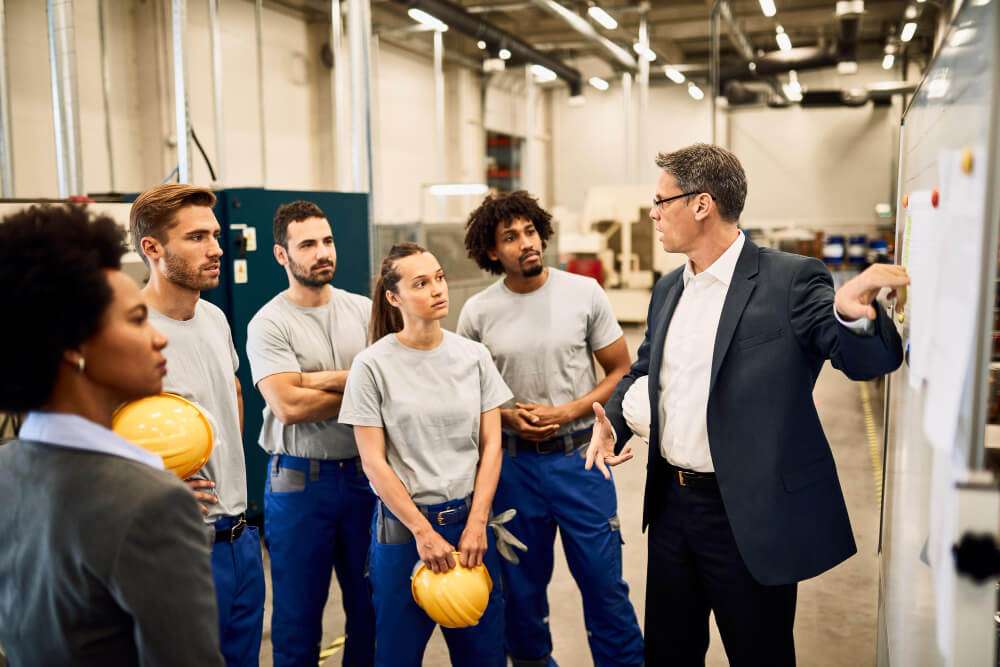
A crucial step in promoting workplace safety is identifying and assessing potential hazards. Conduct regular risk assessments to evaluate the likelihood and severity of threats in your workplace.
This process should involve inspecting the work environment, reviewing past incident reports, and consulting with employees to gather their insights on potential risks.
Implement A Hazard Reporting System
Establish a system for employees to report hazards and safety concerns. This can include a designated email address, an online reporting form, or a physical suggestion box. Encourage employees to report threats and address all matters promptly and effectively.
Perform Job Hazard Analyses
Job hazard analysis (JHAs) involves breaking down specific job tasks and identifying the potential hazards associated with each step.
Conduct JHAs for all job roles within your organization, and use the findings to develop targeted safety procedures and training programs. Regularly review and update your JHAs to account for changes in job tasks or equipment.
3. Implement Effective Safety Controls
Based on the findings of your risk assessments and JHAs, create a set of safety procedures and guidelines tailored to the specific hazards present in your workplace.
These guidelines should cover topics such as the proper use of equipment, safe handling of hazardous materials, and emergency response procedures. Also, include visual aids like color coding clean systems for equipment to ease employees.
Provide Personal Protective Equipment (PPE)
Ensure all employees can access appropriate personal protective equipment (PPE) for their job tasks. This may include safety glasses, gloves, hearing protection, or respiratory protection. For that purpose, you can install PPE Boards in your workplace.
Train employees on the proper use and maintenance of PPE, and monitor compliance with PPE requirements.
Implement Engineering Controls
Where possible, implement engineering controls to eliminate or reduce hazards at their source. This can include installing safety guards on machinery, improving ventilation systems, or redesigning workstations to minimize ergonomic risks.
Utilize Administrative Controls
Administrative controls involve modifying work procedures or schedules to reduce exposure to hazards.
Examples of administrative controls include rotating employees between tasks to minimize repetitive motion injuries, implementing break schedules to reduce worker fatigue, and enforcing strict adherence to safety procedures.
4. Monitor And Evaluate Workplace Safety Performance
Measure your organization’s safety performance by tracking key safety metrics, such as injury rates, near-misses, clean places, and safety training completion rates.
Regularly review these metrics to identify trends and areas for improvement. Besides you can also:
Conduct Regular Safety Inspections
Perform regular safety inspections to ensure that your workplace is free of hazards and that employees follow safety procedures.
Inspections should cover all workplace areas, including storage rooms, break areas, and outdoor spaces.
Review Incident Reports
Thoroughly review all incident reports and conduct investigations into workplace accidents. Use the findings of these investigations to identify the root causes of accidents and implement corrective actions to prevent similar incidents in the future.
5. Maintain Open Communication And Encourage Employee Feedback
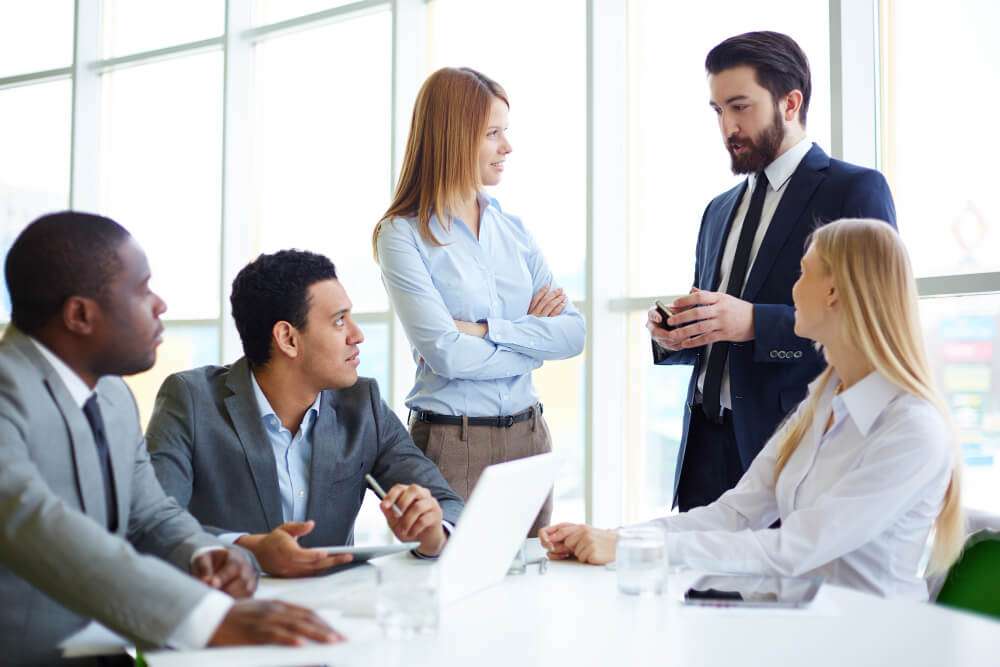
Promote a culture of open communication regarding workplace safety. Encourage employees to voice their concerns and ideas for improving safety. Also, ensure they feel comfortable doing so without fear of reprisal.
Moreover, schedule regular safety meetings to discuss safety-related topics and updates. These meetings allow workers to share their experiences, ask questions, and offer suggestions for improving workplace safety.
Implement a Safety Suggestion Program
Create a safety suggestion program to encourage employees to submit ideas for enhancing workplace safety.
Recognize and reward employees who submit valuable suggestions. Also, consider implementing their ideas if they align with your organization’s safety goals.
6. Stay Informed On Safety Regulations And Industry Best Practices
Stay up-to-date on the safety regulations applicable to your industry and ensure your organization fully complies with the OSHA Act. Regularly review and update your safety policies and procedures to reflect changes in legal requirements.
Furthermore, research and benchmark your organization’s safety performance against industry best practices. Identify areas where you can improve and implement changes to align your safety program with the highest standards in your industry.
Conclusion
Promoting a safe workplace requires a comprehensive approach involving establishing a solid safety culture and implementing adequate safety controls. By following these six steps, you’ll be well on your way to creating and maintaining a safe and productive work environment for your employees.