In today’s fast-paced and ever-changing workforce, businesses continually look for ways to improve their operations and increase efficiency. One popular method for achieving this is implementing lean principles and tools.
One such tool is the 5S Red Tag. While seemingly simple, correctly using this tool can significantly impact a company’s ability to manage inventory and eliminate waste effectively.
In this article, we will explore the ins and outs of 5S Red Tags and how they can be utilized in the workplace.
Understanding the 5S Methodology
Before we dive into the specifics of 5S Red Tags, let’s first gain a clear understanding of the overarching 5S methodology. Originating in Japan, 5S is a continuous improvement approach to organizing the workplace for greater efficiency.
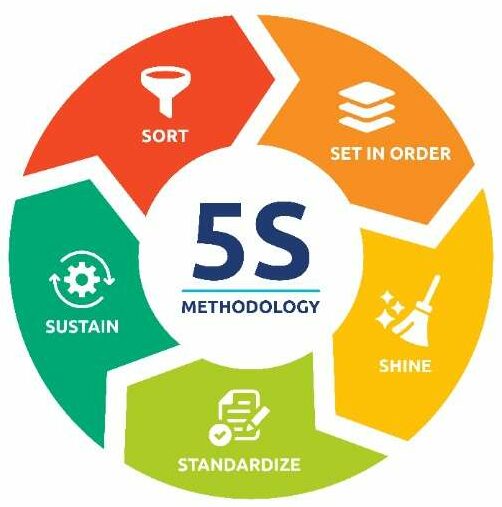
The five S’s in 5S stand for Sort, Set in Order, Shine, Standardize, and Sustain. Each step plays a crucial role in creating a lean and well-organized workspace. Need to know how? Take a look:
- Sort: The first step in the 5S methodology is to sort through all items in the workspace and separate them into essential and non-essential categories. This process helps eliminate clutter and ensures that only necessary items are present, reducing waste and improving efficiency.
- Set in Order: Once items have been sorted, the next step is establishing a proper place for each essential item. By organizing tools, equipment, and materials in a logical and accessible manner, employees can quickly locate and retrieve what they need, reducing the time wasted searching for items.
- Shine: The shine step involves thoroughly cleaning the workspace and equipment. A clean and well-maintained environment improves aesthetics, promotes safety, and prevents equipment malfunction.
- Standardize: To ensure that the gains made in the previous steps are sustained, standardization is crucial. This involves creating clear guidelines, procedures, and visual cues to maintain the organized state of the workspace. Standardization helps establish consistency and ensures that everyone follows the same practices.
- Sustain: The final step in the 5S methodology is to sustain the improvements achieved. This requires ongoing commitment and discipline from all employees. Regular audits, training, and continuous improvement efforts are essential to maintain an organized and efficient workspace.
Now that we have a solid understanding of the 5S methodology, let’s explore the role of 5S Red Tags in the sorting process.
Role Of 5s Red Tags
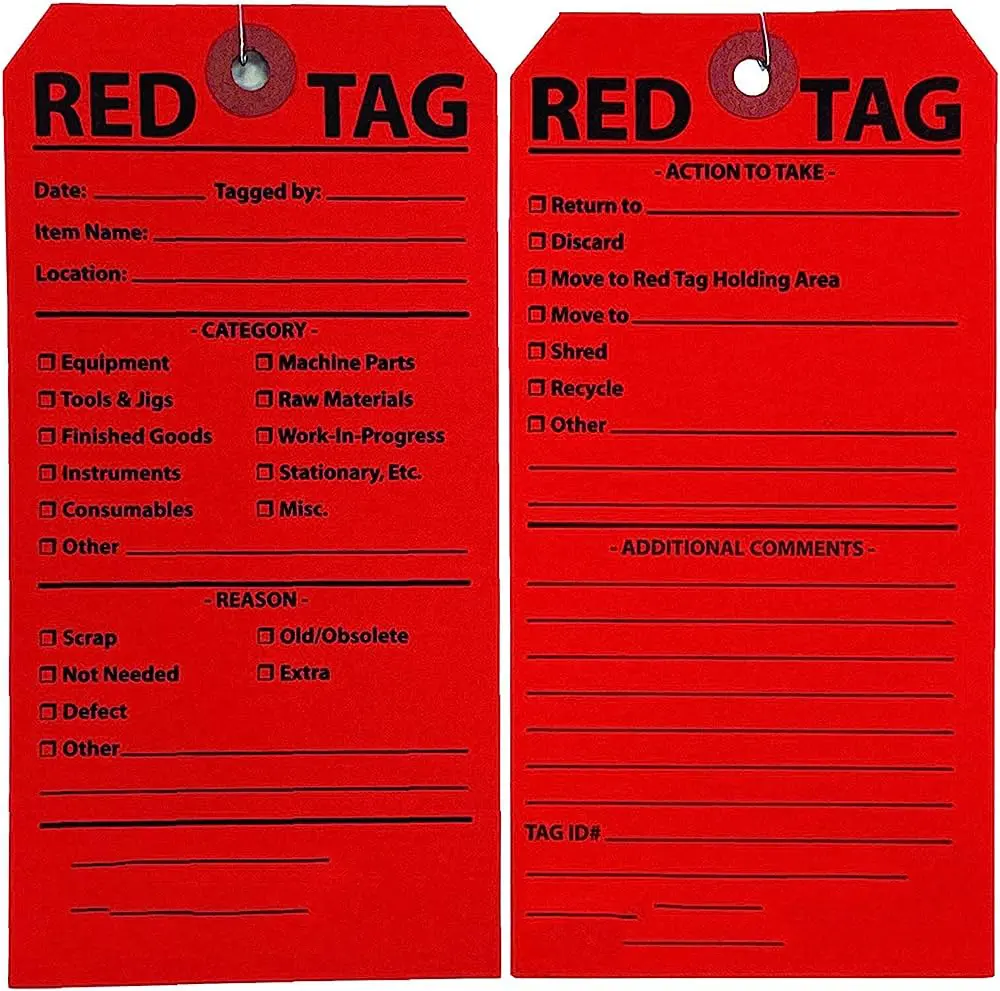
The sorting step of 5S is where 5S Red Tags come into play. The purpose of red tagging is to identify items not needed in the workspace and may be taking up valuable space.
It acts as a visual indicator indicating that an item has been flagged for removal or relocation. Such items may include obsolete tools, machinery, inventory, documents, and even old office chairs.
Proper red tagging transforms the workplace into a more streamlined system with fewer distractions and more space for productive activities. Besides, able to make informed decisions about the disposition of items.
Benefits Of The 5s Red Tag Process
Let’s explore some of the advantages:
- Improved Efficiency: Red tagging allows employees to quickly identify and eliminate unnecessary items, reducing clutter and streamlining workflows. This results in improved productivity and efficiency throughout the organization.
- Optimized Space Utilization: By removing items that are no longer needed, organizations can free up valuable space in their work areas. This enables better organization, reduces the risk of accidents, and improves overall safety.
- Cost Savings: Red tagging helps prevent the unnecessary purchase or replacement of items already available but hidden or forgotten. This can lead to significant cost savings for the organization.
- Enhanced Visual Management: Using red tags as visual indicators enables easy identification of items that need attention. This promotes a culture of accountability and encourages employees to maintain an organized workspace.
- Facilitates Continuous Improvement: The 5S Red Tag process is not a one-time event but an ongoing practice. Organizations can continuously improve their operations and eliminate waste by regularly reviewing and sorting items.
Implementing The 5s Red Tag Process
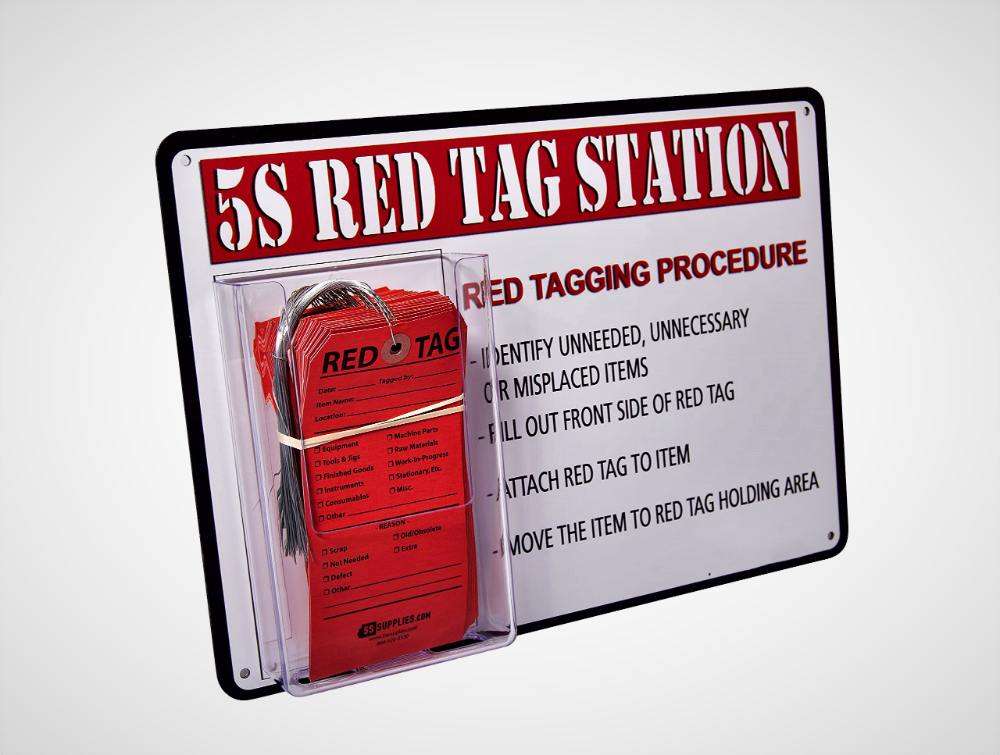
To ensure a successful implementation of this process, it is essential to have a well-thought-out strategy and gain employee buy-in. Take a look at the key steps:
1. Evaluate And Identify Areas For Improvement
Begin by evaluating your workspace and identifying areas that could benefit from the 5S Red Tag process.
This may include storage areas, inventory spaces, workstations, and other areas prone to clutter and disorganization.
By pinpointing these areas, you can focus your efforts and maximize the impact of the red tagging process.
2. Define Red Tag Criteria
Before initiating the red tagging process, establish clear criteria for determining which items should be tagged. This ensures consistency and eliminates subjective decision-making.
Consider item usage frequency, relevance to current processes, and future needs. Communicate these criteria to employees to ensure a unified understanding.
3. Engage And Educate Employees
Employee buy-in is required for the success of the red tag 5s process. Take the time to explain the benefits of the process and address any concerns or questions.
Provide practical training on using red tags and encourage active participation from all employees. Involving employees in the process fosters a sense of ownership and commitment to maintaining an organized workspace.
4. Conduct Regular Red Tag Screenings
It is essential to conduct regular screenings to maintain the benefits of the red tag 5s process. Best practices suggest at least bi-annual screenings, but ongoing implementation as part of the 5S cycle yields the most significant benefits.
Set a schedule for these screenings and communicate it to all employees. Consistency is vital to sustaining the organization’s efforts.
5. Determine Red Tag Holding Period
Establishing a specific timeframe for items in the red tag holding area is essential. Typically, a one to two-month holding period is recommended.
During this time, monitor the usage of tagged items and assess their relevance. Items unused within the holding period should be disposed of or relocated to a designated storage area for seasonal or occasional use.
Conclusion
The 5S Red Tag process is a powerful tool for businesses seeking to optimize their workspace and improve efficiency. By implementing the 5s Red Tag, organizations can eliminate clutter, maximize space utilization, and foster a culture of continuous improvement.
Remember, the success of the 5S Red Tag process relies on clear communication, employee engagement, and ongoing commitment. Embrace the power of 5S Red Tags and unlock the full potential of your workspace organization efforts.