The 5S methodology has entered many different industries, including warehousing. It’s a way of organizing a workspace to be cleaner, more efficient, and more productive. This isn’t just a trendy new buzzword either – data suggest that implementing 5S methodology can reduce workplace injuries by up to 30%, improve supply chain management by 50%, and increase productivity by 15%.
These impressive statistics show that utilizing the 5S method in warehouse management is worth exploring for managers looking to improve their operations and create a safer, more efficient workplace.
This article will explore the fundamental principles of 5S and strategies for implementing it in warehouse management.
Understanding The 5s Methodology
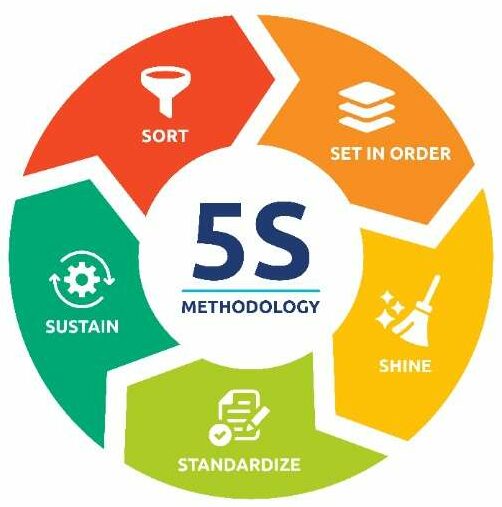
Each “S” represents a pivot step in creating a lean and efficient warehouse environment. Take a look and see how they contribute to warehouse optimization.
1. Sort
Sorting is the foundation and sets the stage for the subsequent steps of the 5S methodology. It involves systematically evaluating and categorizing items within the warehouse to determine what is necessary and what is not.
By eliminating clutter and unnecessary items, warehouses can create a more streamlined and efficient workspace. Sorting also helps identify redundant inventory, obsolete equipment, and things that impede workflow.
2. Set In Order
This step aims to determine the optimal location for each item based on the frequency of use and workflow requirements. By strategically organizing items and creating designated storage areas, warehouses can minimize search time, reduce errors, and improve productivity.
Visual cues such as color-coded labels, signage, and floor markings can further enhance organization and ensure consistent adherence to the established order.
3. Shine
A clean and well-maintained warehouse improves aesthetics, operational efficiency, and employee morale. The shine step involves regular cleaning and maintenance to keep the workspace clean and debris-free.
This includes sweeping, dusting, sanitizing surfaces, and inspecting and maintaining equipment. A clean and orderly warehouse promotes a positive work environment, enhances safety, and minimizes potential hazards.
4. Standardize
This step involves implementing standardized procedures, guidelines, and protocols to ensure consistency and accountability.
By establishing clear expectations and providing training on best practices, warehouses can maintain the gains made in productivity, organization, and cleanliness.
Regular audits and performance evaluations help identify areas for improvement and reinforce the importance of adherence to standardized processes.
5. Sustain
This step is all about long-term commitment and continuous improvement. Sustaining the achieved improvements requires ongoing monitoring, evaluation, and adaptation.
Warehouses must foster a culture of continuous improvement, where employees are encouraged to identify opportunities for enhancement and actively participate in problem-solving.
Regular assessments of key performance indicators, feedback loops, and employee engagement initiatives can contribute to sustained success.
Why Does Implementing 5S in Warehouse Management Make Sense?
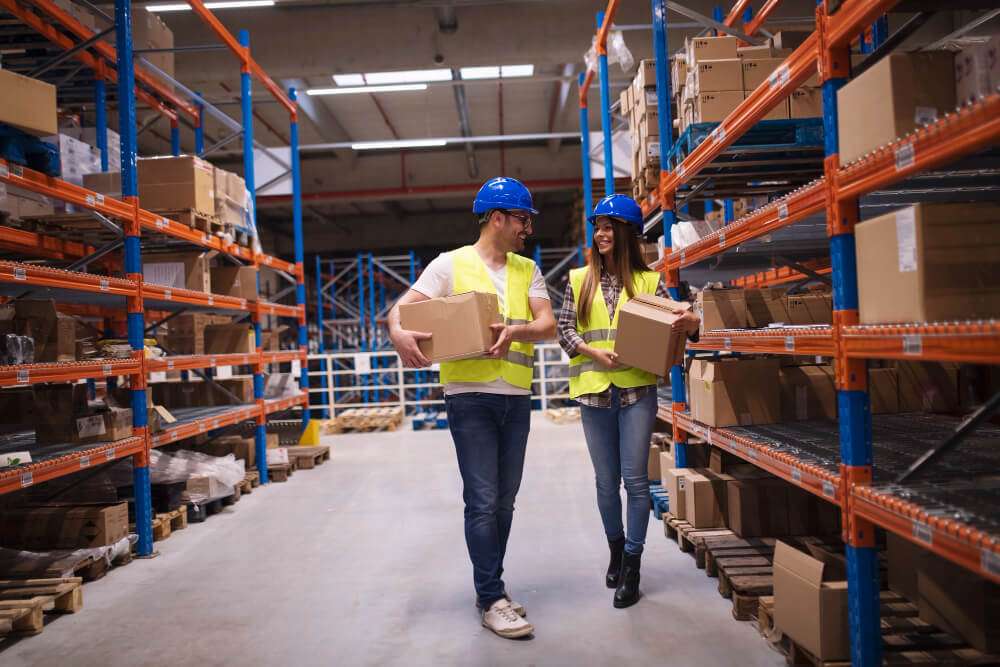
Implementing the 5S methodology in warehouse management offers many benefits that can significantly improve overall operations. Take a look at how implementing 5S make sense:
1. Enhanced Productivity
One of the primary goals of the 5S methodology is to increase productivity by eliminating waste and optimizing workflow.
By removing unnecessary items, organizing tools and materials, and standardizing processes, employees can work more efficiently, resulting in higher productivity.
2. Improved Safety
A clean and well-organized workspace is essential for ensuring the safety of employees.
The 5S methodology helps identify and eliminate potential hazards, such as cluttered walkways, improperly stored materials, or equipment malfunctions. Promoting a safe working environment significantly reduces the risk of accidents and injuries.
3. Cost Reduction
Warehouse managers can minimize storage costs by optimizing space utilization and reducing unnecessary inventory. Besides, streamlined processes and improved efficiency result in lower labor costs and reduced downtime.
Thus, the 5S helps eliminate wasteful practices and maximizes resource utilization, leading to significant cost savings.
4. Quality Improvement
By reducing clutter and implementing standardized processes, the chances of errors and defects are minimized.
This leads to higher customer satisfaction, increased customer loyalty, and a better overall reputation for the warehouse.
Guide To Implement 5S In Warehouse
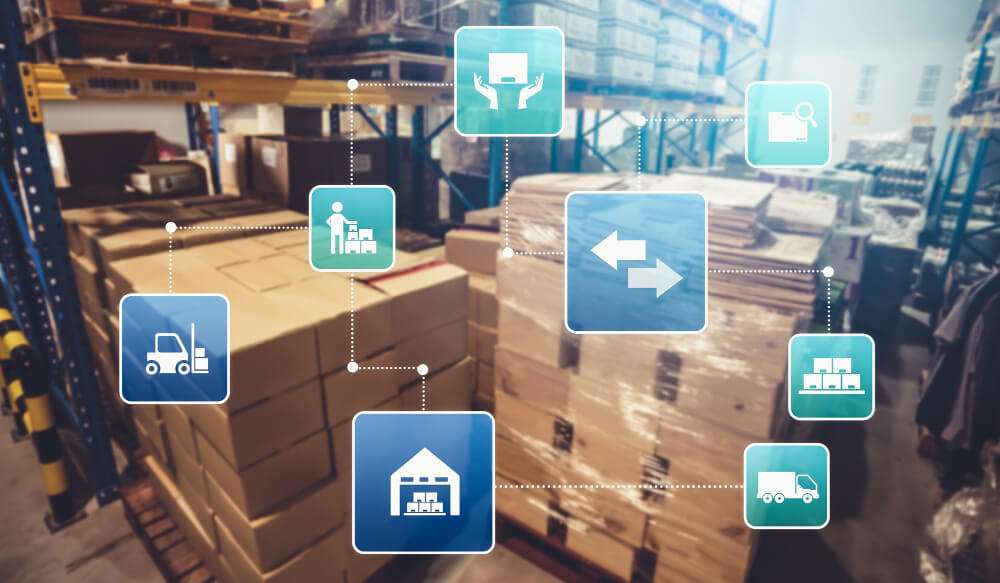
Now that we know why implementing 5S in a warehouse makes sense, let’s explore how to implement these principles to optimize their operations.
1. Define Clear Goals
Before embarking on the 5S journey, it is necessary to define clear goals and objectives. Identify:
- What do you hope to achieve through implementing the 5S methodology?
- How does it align with your overall warehouse management strategy?
This will provide a roadmap for the implementation process and help measure the success of your efforts.
2. Start Small and Prioritize
Implementing the 5S in large warehouses with complex operations seems a tough nut to crack. To ensure success, starting small and focusing on specific areas or processes with the most significant impact is advisable.
By prioritizing key areas for improvement, warehouses can create a sense of accomplishment and momentum, which can then be applied to other areas in subsequent implementation phases.
3. Involve Employees
Employee involvement is essential for the successful implementation of 5S. Engage your workforce by providing training on the principles and benefits of 5S and actively seeking their input and feedback.
Employees who understand the purpose and value of 5S are more likely to embrace the changes and take ownership of maintaining a clean and organized workspace.
Encourage employees to identify opportunities for improvement, share their ideas, and collaborate on implementing solutions.
4. Establish Visual Management Systems
Visual management systems play a crucial role in the 5S. Use color-coded labels, floor markings, signage, and visual cues to guide employees in locating items, identifying storage areas, and understanding workflow processes.
Clear and consistent visual communication reduces errors, minimizes search time, and enhances efficiency. Regularly review and update visual management systems to remain relevant and practical.
5. Regular Audits and Inspections
To sustain the 5S practices, it is vital to conduct regular audits and inspections. These evaluations help identify areas of improvement and ensure compliance with the established procedures.
It also provides opportunities for employee feedback. So, use the insights gained from audits to refine and enhance the 5S practices in your warehouse continually.
6. Foster an Improvement Culture
The 5S methodology is not a one-time implementation but a continuous improvement process. Foster a culture of continuous improvement by encouraging employees to identify areas for enhancement and propose innovative solutions.
Recognize and reward employees who actively contribute to the ongoing success of the 5S practices.
7. Establish Standardized Procedures
Develop clear procedures and guidelines for each of the 5S steps and ensure that they are communicated effectively to all employees.
Regularly review and update these procedures to accommodate changes in the warehouse environment and evolving best practices.
Conclusion
The 5S offers a robust framework for optimizing warehouse management and boosting productivity. By implementing the 5S principles, warehouses can eliminate waste, improve safety, reduce costs, and enhance overall quality.
Successful implementation requires clear goals, proper training, standardized procedures, regular audits, and a culture of continuous improvement. Embracing the 5S methodology can transform warehouses into highly efficient and productive environments, setting the stage for long-term success in the dynamic world of modern logistics.