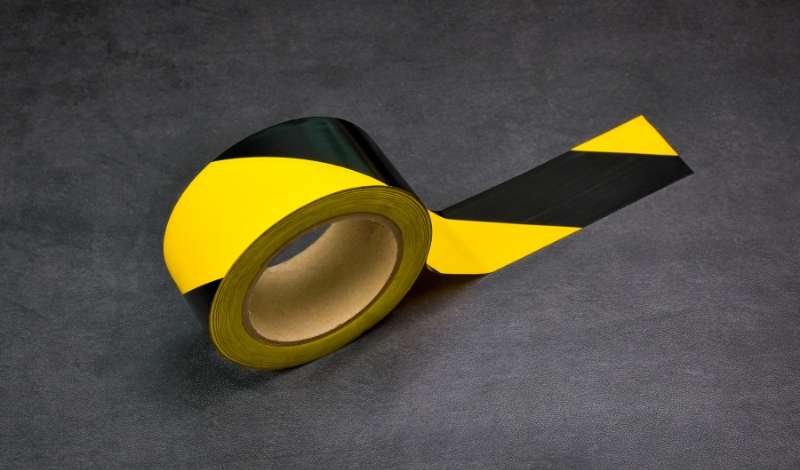
Your shop floor is a hub of activity, bustling with employees, equipment, and forklifts. This constant movement, essential for your business, also poses risks for employee injuries.
To mitigate these risks, it’s crucial to implement a comprehensive floor marking strategy. Following the Occupational Safety and Health Association (OSHA) guidelines, you should clearly delineate permanent aisles and passageways with floor marking tape.
Enhancing this basic requirement with a 5S floor marking guide can significantly improve safety and efficiency. This expanded approach involves integrating Lean/5S, visual workplace principles, and a standardized color-coding system to create a safer, more organized, and more efficient workspace.
Optimizing Workplace Efficiency with 5S Floor Marking
A standardized 5S floor marking color system in your facility can significantly enhance efficiency and safety. By associating specific colors with particular areas or actions, employees can navigate the facility more quickly and efficiently, aiding in task completion and resource location.
This color-coded approach offers several benefits:
- Improved Safety and Emergency Guidance: Utilizing floor tape to delineate aisles and exit paths clearly marks the safest routes through the facility, safeguarding both pedestrians and forklift operators. In emergencies, this also provides rapid evacuation directions.
- Enhanced Organizational Structure: Demonstrating connections through color-coding, such as marking a cart and its storage area with matching colors, helps employees quickly identify when items are out of place.
- Direct Communication of Crucial Information: Consistently marking hazards with bright colors, like red or yellow, conveys essential safety information right where it’s most needed.
- Boosted Employee Productivity: Employees save time by not having to search for items or locations. For instance, recognizing the color-coded floor marking for a specific material storage area allows for quicker location identification.
Compliance and Best Practices in Workplace Marking
Numerous Occupational Safety and Health Association (OSHA) regulations clearly distinguish permanent aisles and passageways.
However, more government-enforced or universally recognized industry standards need to specify which colors should be used for floor markings.
Nonetheless, several relevant standards in workplace visuals necessitate or suggest the implementation of floor marking and color coding. For instance, have a look at these 5S floor marking guidelines below:
Mechanical Equipment Operations
- OSHA §1910.176(a): This regulation emphasizes the importance of maintaining clear and safe clearances in areas where mechanical handling equipment is used. This includes aisles, loading docks, doorways, and areas requiring navigation or passage. Keeping these aisles and passageways clear, well-maintained, and free from obstructions that could pose hazards is mandatory. The rule also stipulates that permanent corridors and halls must be clearly marked.
Fire Extinguisher and Safety Markings
- General Environmental Controls, §1910.144: The guideline specifies red as the primary color for identifying fire protection equipment, apparatus, containers of flammable liquids, emergency stop buttons, and electrical switches.
- §1910.144(a)(1): Reinforces red for fire protection equipment and apparatus.
- §1910.144(a)(3): Designates yellow to indicate caution and mark physical hazards.
Egress Path Marking
- Means of Egress, §1910.35: Compliance with NFPA 101, Life Safety Code, or the 2009 edition of the International Fire Code (IFC) regarding exit routes is considered as adherence to OSHA’s §1910.34, §1910.36, and §1910.37.
Aisle Definition with Floor Marking Tape
- Letter of Interpretation, §1910.22(b): This interpretation allows for flexibility in the color and design of lines delineating aisles as long as they clearly define the area as aisle space. This can include patterns like dots, squares, strips, or continuous lines, with a recommended width ranging from 2 to 6 inches.
International Fire Code 2009 Provisions
- BradyGlo Floor Marking Tape, §1024.1: Requires approved luminous egress path markings for buildings with floors over 75 feet above the lowest fire department vehicle access level.
- §1024.2.1: Mandates a solid and continuous stripe along the horizontal leading edge of each step, covering the entire step length.
- §1024.2.4: Specifies that perimeter and floor-mounted demarcation lines should be placed close to walls and extended near the markings on the leading edges of landings, with specified width and interruption guidelines.
5S Floor Marking Color Guide
To maintain an organized and safe workspace, applying floor markings requires a color-coding system that’s easy for workers to remember and reduces the variety of marking materials needed. Here’s a simplified floor-marking guide of color-coding:
- Yellow: Designates aisles, traffic lanes, and work cells, serving as employee navigational guides.
- White: Identifies equipment and fixtures not already marked by other colors, such as workstations, carts, and shelving units.
- Orange: Signals that materials or products are in a holding pattern, pending inspection.
- Red: Alerts to areas of concern such as defects, scrap, rework stations, and red tag areas where items are marked for removal or attention.
- Blue/Green/Black: Marks areas related to materials and components, categorizing raw materials, items in process, and finished goods.
- Photoluminescent: Highlights steps and perimeters, specifically for marking egress paths in emergencies when lights are out.
- Red and White Stripe: Indicates zones that must remain clear for safety and compliance, especially in front of electrical panels, firefighting equipment, and other safety-related areas.
- Black and White Stripe: Delineates spaces that should be kept open for operational efficiency, not necessarily for safety or compliance reasons.
- Yellow and Black Stripe: Warns of potential physical or health hazards, ensuring that employees are aware of risks in the vicinity.
Additional Relevant Floor-Marking Guide Standards
In the realm of workplace safety and organization, various standards point to the necessity of utilizing markings and color codes:
ANSI Safety Signage Colors
The ANSI Z535.1 Safety Color Code is often cited as a reference for floor marking. Although previous editions, like ANSI Z353.1-1998, included color codes for safety hazards and equipment, these were not carried over to the 2002 edition.
The current standard, particularly in Section 4.2, clarifies that its color specifications are tailored for safety signs and should not be applied to floor markings.
OSHA Hazard Marking Colors
References to OSHA’s 29 CFR 1910.144, which outlines the Safety Color Code for Marking Physical Hazards, are also common. This standard provides limited guidance and is not intended for floor marking color usage.
According to this code, red is designated for fire protection equipment, emergency stop devices, and containers of hazardous materials. At the same time, yellow is assigned to mark physical hazards that could cause impacts, trips, falls, or entrapment.
Conclusion
In conclusion, while OSHA mandates the clear distinction of aisles and passageways, specific government or industry-wide standards for floor marking colors are absent. Organizations may look to ANSI for guidance on safety signage, but it’s clear that its recommendations are not intended for floor marking.
Companies can create a safer, more organized, and efficient work environment by choosing a simple and intuitive color scheme, such as the one outlined in our guide. The key is consistency and clarity in using these visual cues to ensure that all employees understand and benefit from the color-coded system.
Read more: 5s In The Warehouse: Why It Makes Sense