
Lean methodology has taken the world by storm and for good reason. It’s all about streamlining processes, reducing waste, and improving efficiency, ultimately leading to a more productive and profitable organization.
One of the key components of a successful lean implementation is the usage of visual controls. In this blog, we’ll dive into the world of visual controls and explore five types that can revolutionize your business operations. So let’s get started!
What is Visual Control?
Visual control is a communication device used in the work environment that tells us at a glance how work should be done or how mistakes should be avoided.
It is a powerful tool in lean management, allowing employees to understand quickly:
- The status of a project
- Identify problems
- Make informed decisions based on facts
Visual controls are essential for maintaining efficiency, minimizing waste, and meeting quality standards in a lean workplace.
The Importance Of Visual Controls In Lean
Visual controls play a crucial role in implementing lean principles within an organization. They provide
- A clear and concise way for employees to understand their tasks, track progress, and identify potential problems
- Help standardize decision-making based on facts
- Streamlining processes and improving overall efficiency
- It can be applied across various departments. Making them a versatile tool for any organization looking to adopt lean practices
Types of Visuals Control
Take a look at the five essential types of Visual Control for the workspace:
1. Color Coding
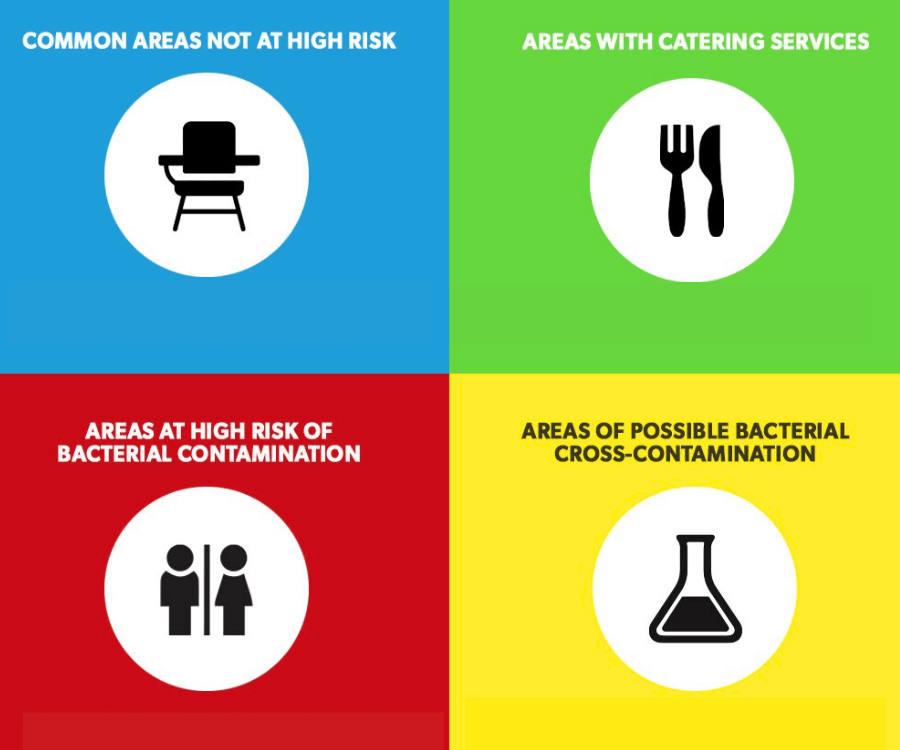
Color coding is one of the simplest and most effective visual controls that can be applied across various industries and departments.
By using different colors to represent specific statuses, categories, or actions, employees can quickly understand what actions they need to take. Thus no need for verbal communication or lengthy explanations.
Benefits
- Consistent and uniform style across the organization
- Easy to understand and implement
- Applicable to various departments and industries
Examples
- Color-coded shadow boards for tools in a manufacturing facility
- Floor markings indicating pathways, work zones, or safety areas
- Office documents are categorized by color for easy navigation and organization
2. Andon Systems
Andon systems are a form of visual control that alerts management, maintenance, and operators to potential problems or issues within a process. It can be used in various settings, from manufacturing floors to office environments.
They allow team members to quickly notify support staff when problems arise, ensuring that issues are addressed immediately.
Benefits
- Rapid identification and resolution of problems
- Improved communication between team members and support staff
- Applicable to both manufacturing and office environments
Examples
- Manufacturing facilities use Andon lights to signal machine malfunctions or part shortages.
- A green light may indicate that everything is running smoothly, while a red light may signal a problem that needs attention.
- Office environments use flags or indicators to signify process issues that need immediate attention. Makes it easy for managers and team members to monitor progress and identify bottlenecks.
3. Standard Work
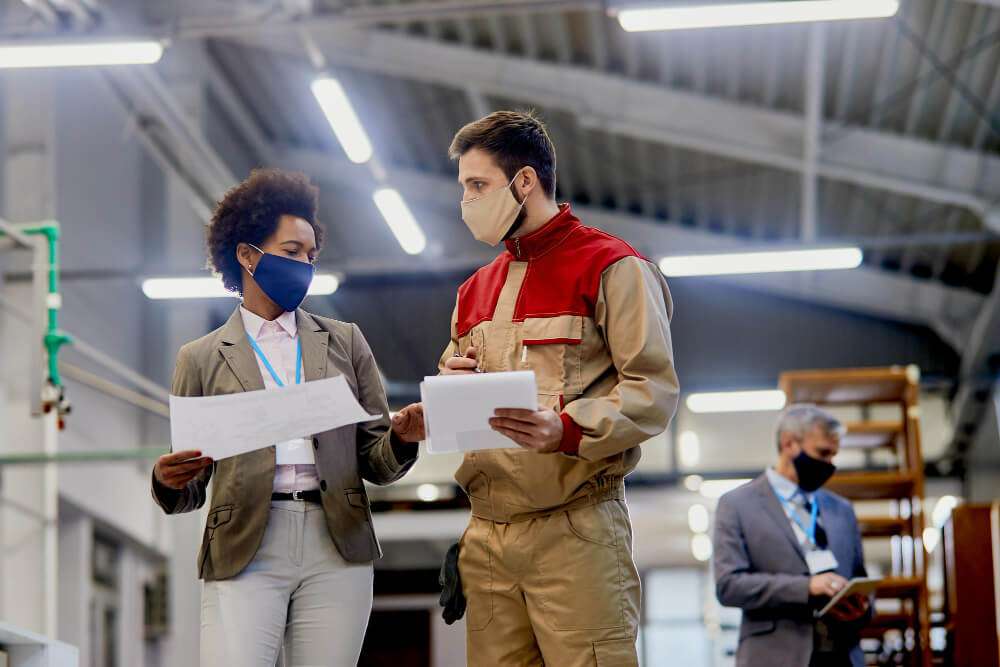
Standard work is a set of documented procedures that outline the most efficient way to perform a task.
It gives employees a clear understanding of the tasks they must complete and determine the appropriate steps and timing for each task. This ensures that all team members work effectively on the same page.
Benefits
- Provides structure and predictability to employees’ work schedules
- Maximizes efficiency and impact
- Ensures consistent outcomes in terms of quality, safety, and output
Examples
- Work instructions, such as charts or diagrams, can help employees understand the correct sequence of steps at each work cell in a manufacturing facility
- Standard worksheets with instructions and diagrams for various processes. This ensures all employees follow the same best practices, promoting consistency and reducing variability.
4. Floor Line Marking & Signage
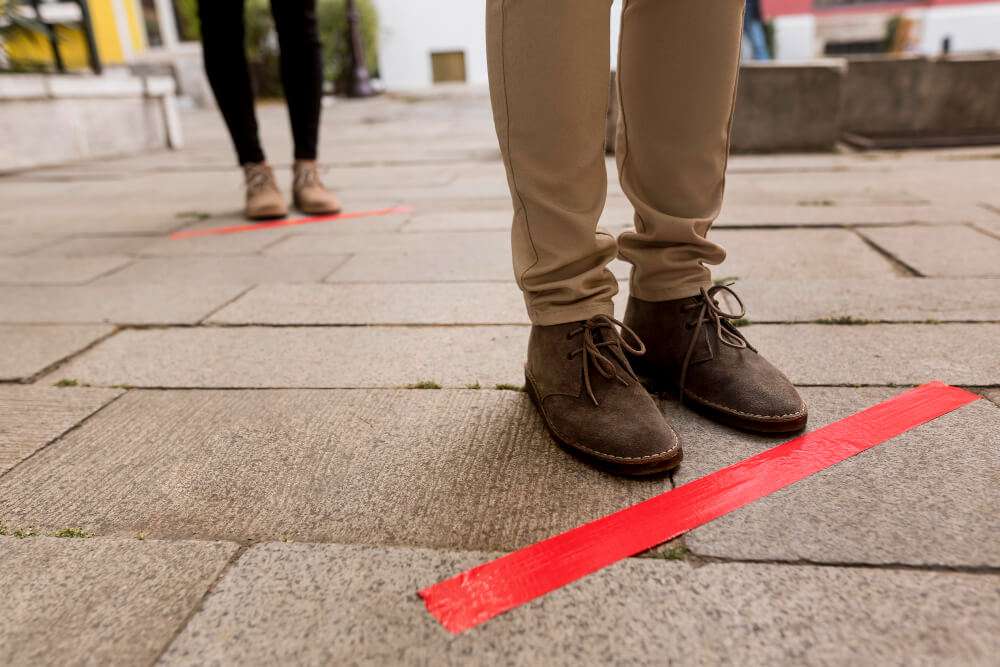
Floor line marking and signage are essential visual controls that help employees understand where they should be and what they should be doing in the workplace. It outlines pathways, vehicle lanes, work cells, and intersections within a facility.
These markings and signs ensure that materials and people flow seamlessly throughout the workspace, promoting safety and efficiency.
Benefits
- Enhances safety and organization within the workplace
- Provides clear pathways and direction for employees
- Promotes efficient material and people flow
Examples
- Color-coded floor markings indicating different zones or pathways in a manufacturing facility
- Signage directing employees to specific work areas or safety stations
5. Kamishibai Board & Tee Cards
Kamishibai boards and tee cards are visual controls that allow employees to determine if a task has been completed or not quickly.
These simple yet effective tools can be used in manufacturing and office environments. It ensures that team members are always aware of the status of their tasks.
Benefits
- Quick and easy way to track task completion
- Promotes a culture of continuous improvement
- Applicable to various industries and departments
Examples
- Manufacturing facilities using Kamishibai boards to track production tasks and progress
- Office environments utilizing tee cards to manage project timelines and milestones
6. Additional Visual Controls For Quality And Safety
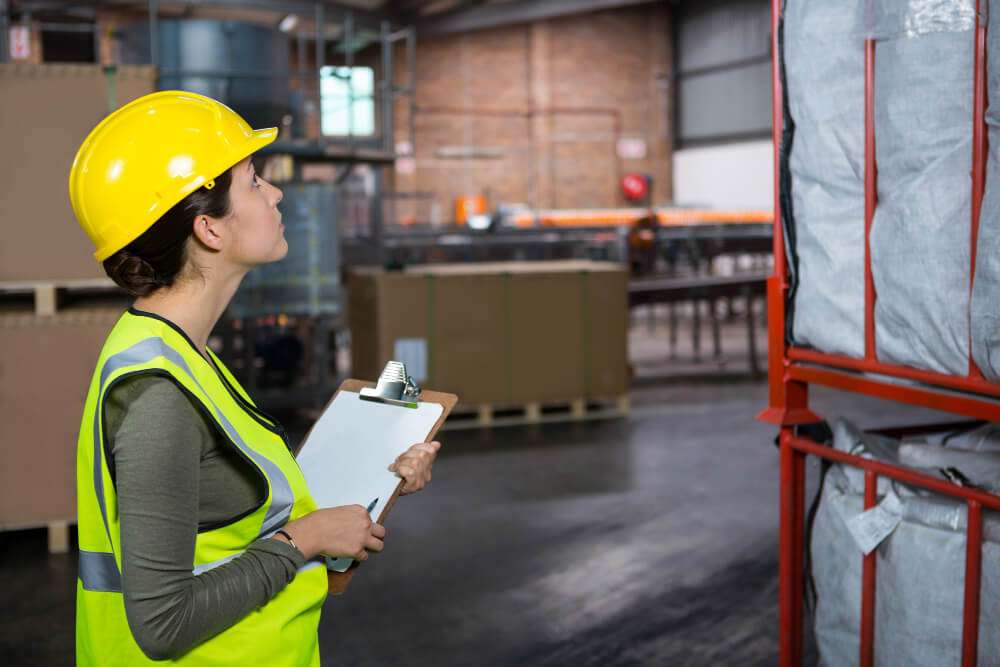
Visual controls can also play a significant role in maintaining quality and safety within an organization. Some examples of visual controls that support these objectives include:
- Quality standards and visual references for operators to ensure product consistency
- Safety signage and indicators to promote a safe working environment
Conclusion
By adopting visual controls in your organization, you’ll be taking a significant step towards implementing lean principles and reaping the benefits that come with them. Visual controls can revolutionize your business operations and lead you to success. It can do everything from increased efficiency and reduced waste to improved communication and collaboration. So, implement these five types of visual controls in your organization today and witness the transformative power of lean methodology.